If you ever happen to be on Hong Kong Island and you pass a long haired Dutchman rocking black and white shoes that look straight out of the future or an anime you grew up with, you’ve likely just encountered Philippe Holthuizen. And as for the sneakers you witnessed, those are from his own inimitable brand of 3D printed sneakers, called
FUSED Footwear.
Philippe’s journey originally started in Transportation Design at the Design Academy in the Netherlands, followed by a Master’s degree in Barcelona. But he soon realized that the car designer lifestyle didn’t suit him. After five years of research, design, iteration and personal wear-testing, the one-man operation is the culmination of an extensive career originating in automotive design that eventually led him to realize the yet untapped potential for recyclable 3D printed footwear.
Nate recently headed to Maker Hive in Kennedy Town, Hong Kong to sit down with the brand founder and footwear designer to learn more about how a 3D-printed speaker gets made and to hear his insights on the tech, the industry and the culture around self-starting makers.
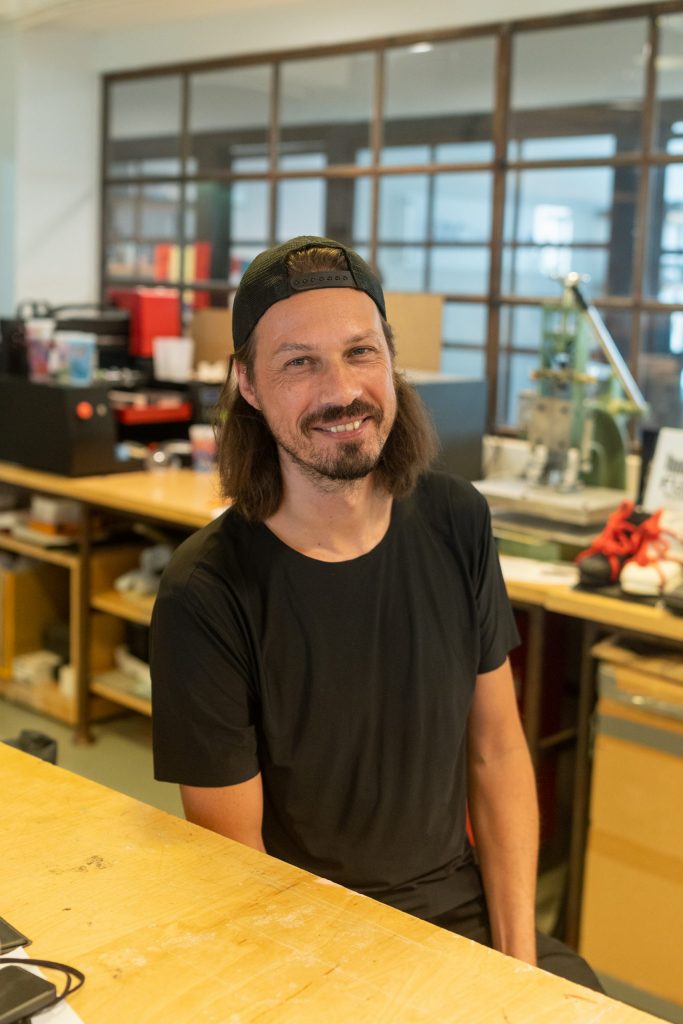
Philippe works out of both his studio on Lamma Island and his space at MakerHive.
The Founder
Can you tell me a bit about yourself and your design background?
I’m Philippe Holthuizen. I’m a product designer who turned into a footwear designer who turned into an entrepreneur. I 3D print shoes and hopefully at some point, I’ll make that my life’s income.
You spent quite some time training to be a car designer. Could you tell me a bit about that journey and what is it about footwear design that felt like a logical next step?
Growing up in Holland, we had the Design Academy, which was very well known for how conceptual it is and was, and that’s where I started. I studied Transportation Design and did a direction called Man&Mobility. In terms of working toward going into car design, it was the closest option for where I was in Holland at the time.
It was great fun, but also very conceptual. It actually took me six years instead of the four years that most people take because I wasn’t the best fit; I was a bit too practical for that school, maybe.
I followed that up with a Master’s degree in Barcelona, also in Transportation Design, again, still wanting to be a car designer. Barcelona was super fun. It’s an awesome city. I learned Spanish. I made some friends from all over the world and did some really nice student projects, but I realized at the end I probably shouldn’t be a car designer. So I went back to Amsterdam for another six years there.
As for footwear, I would say it’s the same thing as what attracted me to car design. It’s all about the flow, proportion and shape of the product (car or shoe) while still having to fit the practical purpose.
I think it has to do with the fact the aesthetics are very important, but they also have to be very practical. That puzzle is what is most interesting. On the one hand, you’re making a sculpture and on the other, it has to be a comfortable or working sculpture, which is the big part that attracted me given my skill set with 3D.
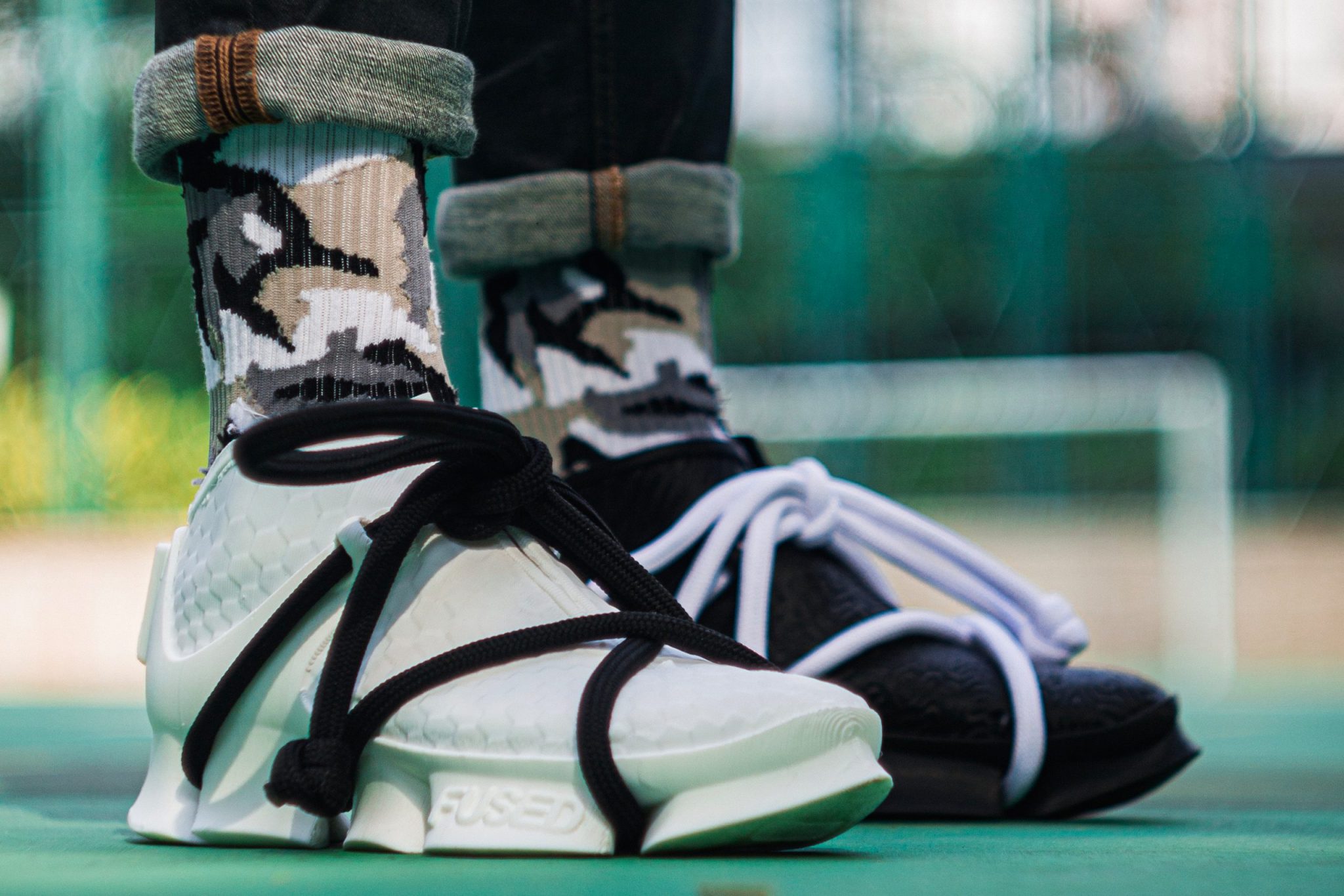
The FUSED Kodo: available in black, white or mixed. The left upper features a coral pattern, while the right shoe has a scaled pattern in reference to the relationship between Water and Fire.
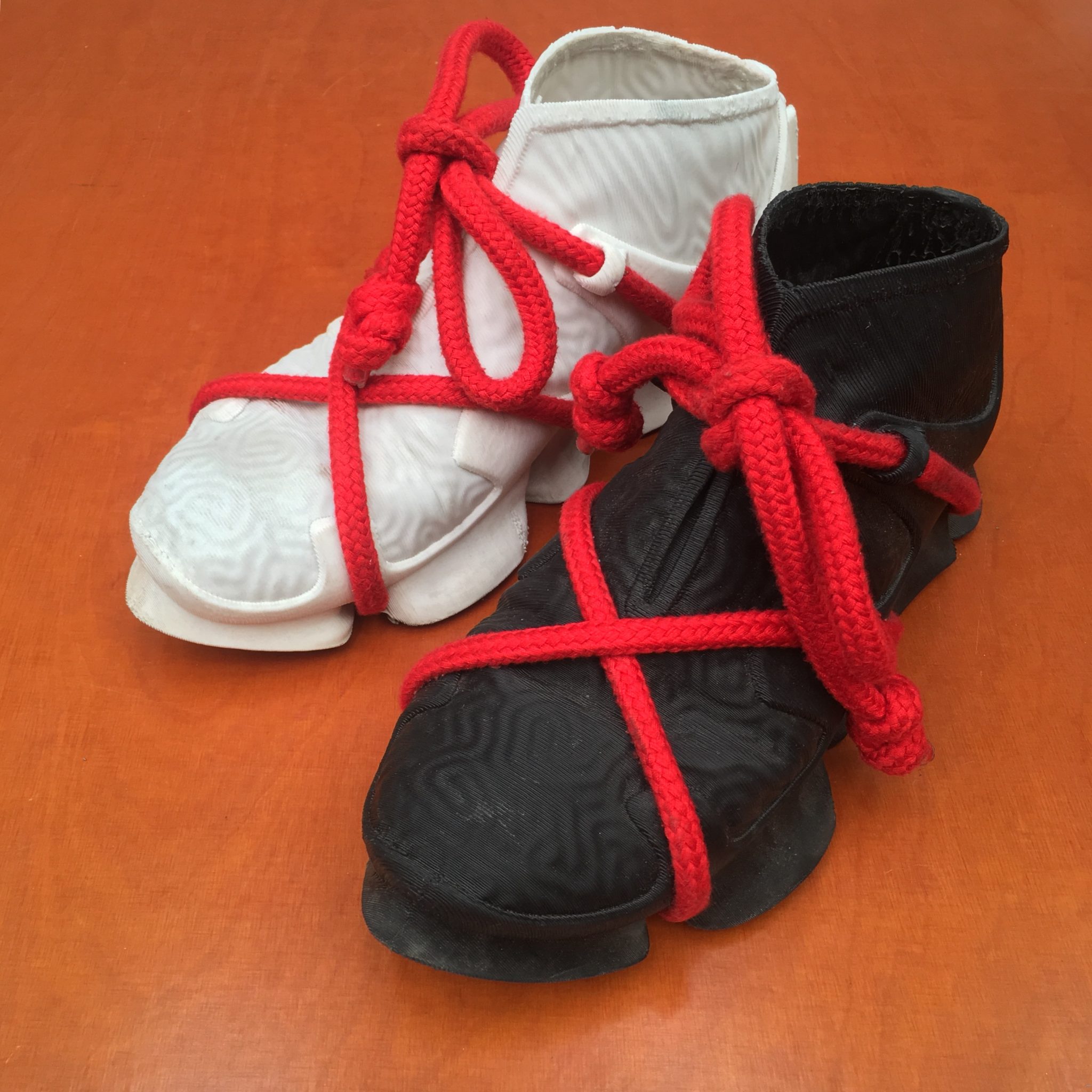
The coral-pattern of the Kodo, modeled after brain coral.
Could you tell me a bit about your time designing at United Nude?
While I was back in Amsterdam, I worked for a couple of design studios, but there wasn’t anything that really grabbed me.
And then on Dezeen, I saw an internship at United Nude, which is a Dutch footwear brand that’s definitely doing very avant-garde stuff. I was like, “that’s a super cool brand.” So I just applied.
I was over 30 at that point, which is not a typical internship age. But the creative director and the owner, Rem D Koolhaas, was like, “oh, but you can do 3D CAD. That’s actually what we can use because we’re doing a lot of injection molding.”
I went there for three months and that turned out to be great, so I stayed for three years. We did some really cool stuff because at the time, United Nude was doing a lot of shoes for Iris van Herpen and we also did some designs for Zaha Hadid. These were the type of shoes you don’t usually get to do, if you come from a traditional shoe designer background.
With a more traditional background, you would communicate your designs as Tech Packs (Technical Packets or Specification Sheets) and so you’d make 2D drawings of what the shoe should look like. That goes to a factory and then they’ll try to make your design into reality. As a 3D designer, however, I designed stuff directly in 3D and whatever I designed could almost be directly interpreted by the factory without needing that back and forth.
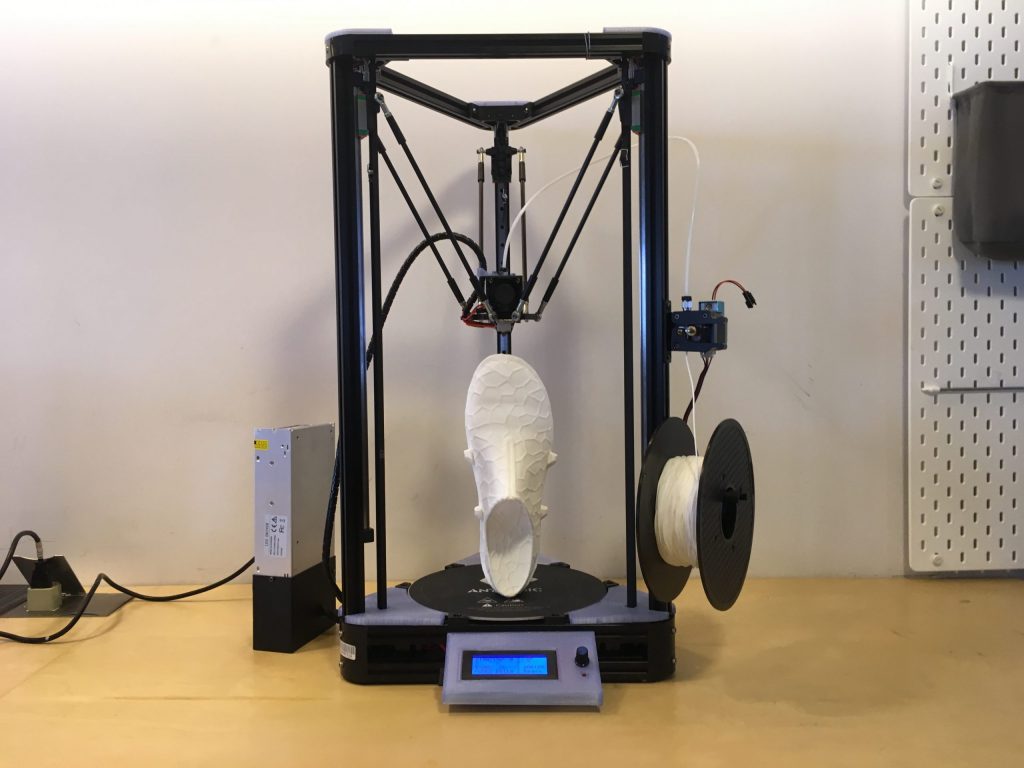
3D printing a FUSED sneaker via Fused Deposition Modeling (FDM), which involves countless layers of hardwearing Thermoplastic Elastomer (TPE) filament.
The Beginning of FUSED
Could you walk me through the timeline that lead to how FUSED came to be?
On one hand, it’s about how I found my passion and my goal in life, but also how it happened super organically, which is really funny.
After United Nude, I went to Singapore to do a startup centered around kitchen appliances. But because I’d leveled up and on a startup budget, there weren’t enough resources for a full team, I was the design director and that also meant I had to do all the branding by myself. That meant I got to learn the graphic side of a brand in terms of photography, marketing, and the like.
Hong Kong was right next door and I had a friend here that wanted to do something with 3D printing so I came over in 2016. The idea was we’re in the tropics where people like wearing open shoes, you can’t put an orthopedic insole in an open shoe, so we thought it would be interesting to do fashionable orthopedic sandals. Unfortunately, it didn’t work out, again because we couldn’t raise enough money.
But that basically led to me seeing the potential of 3D-printed footwear, and that’s what I’ve been doing for the last five years.
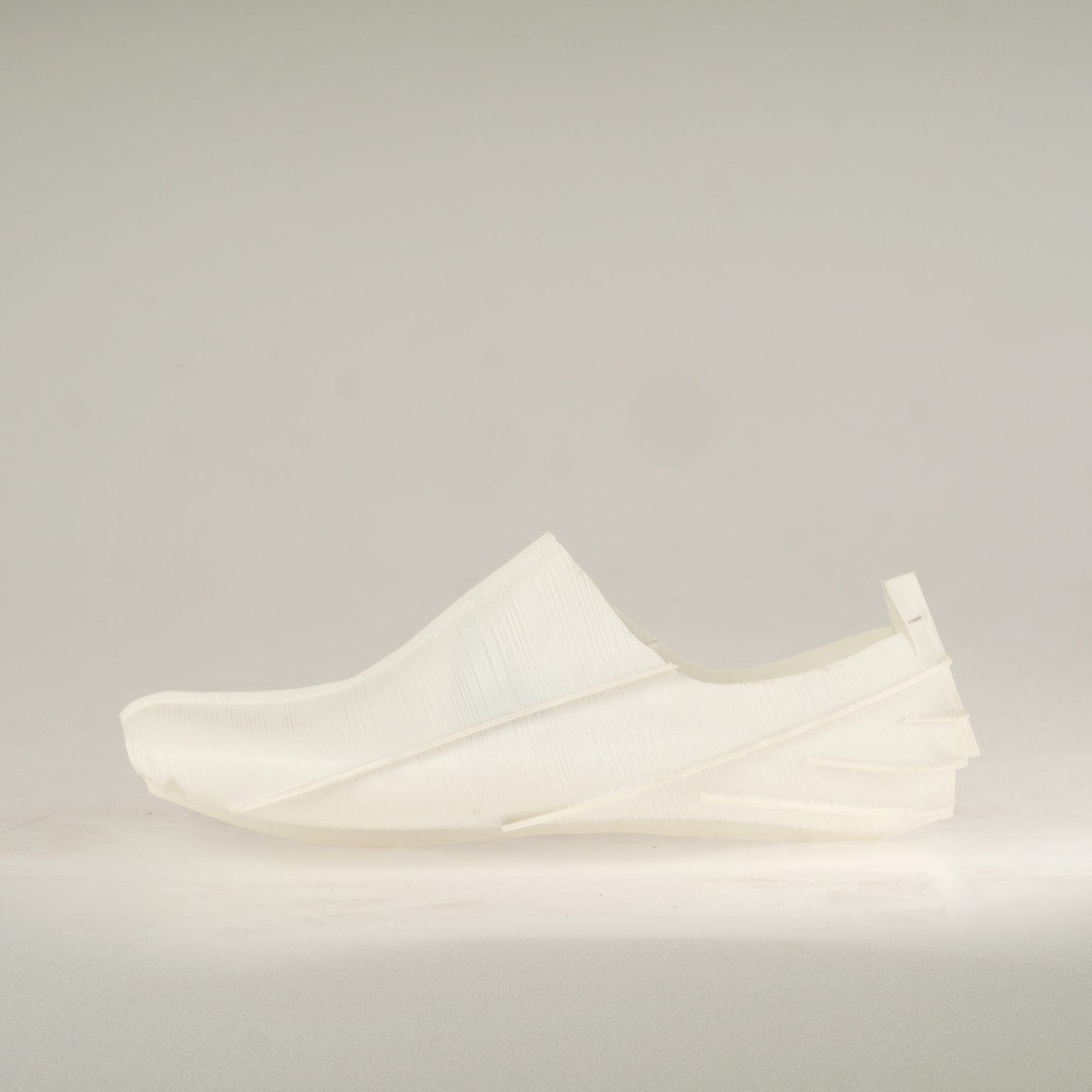
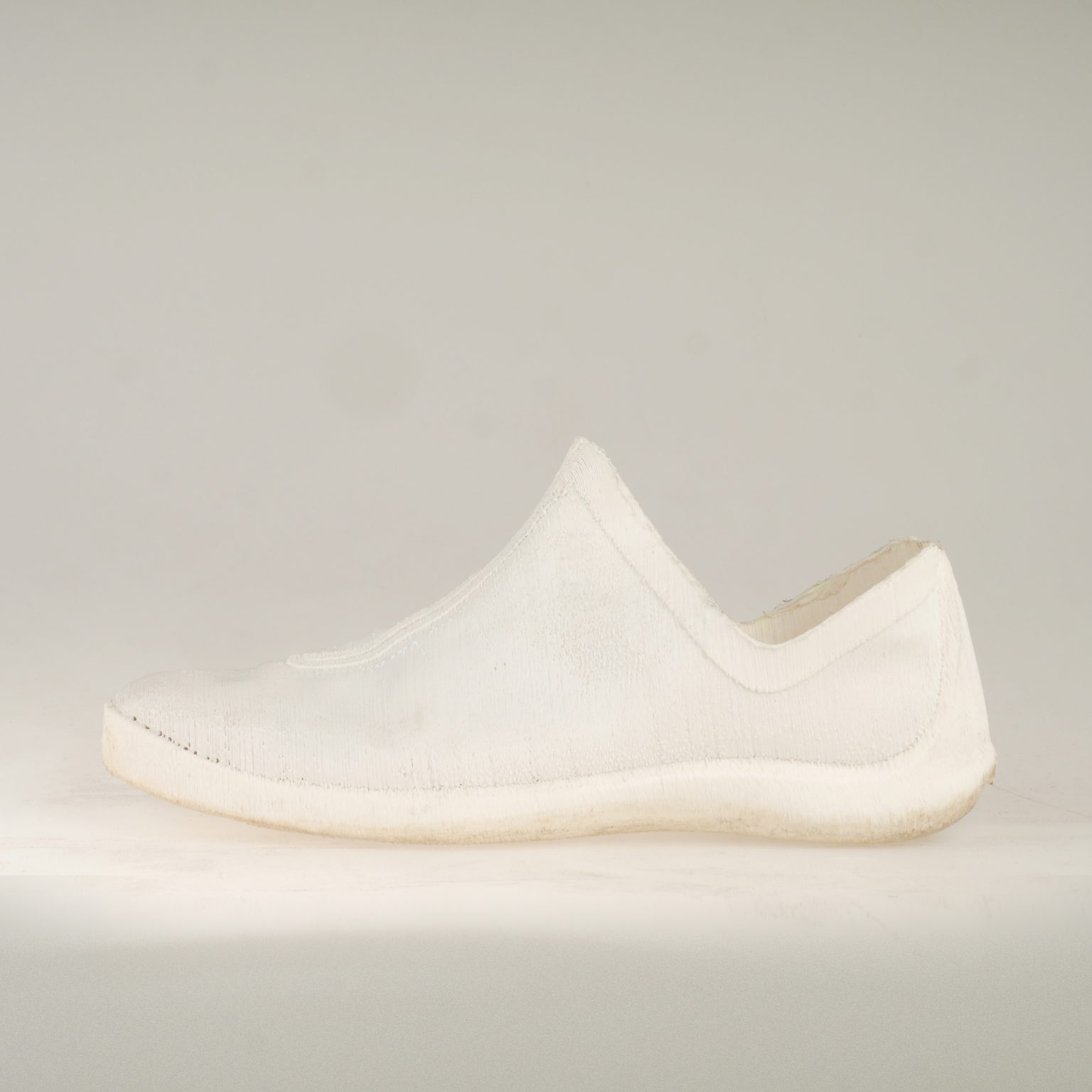
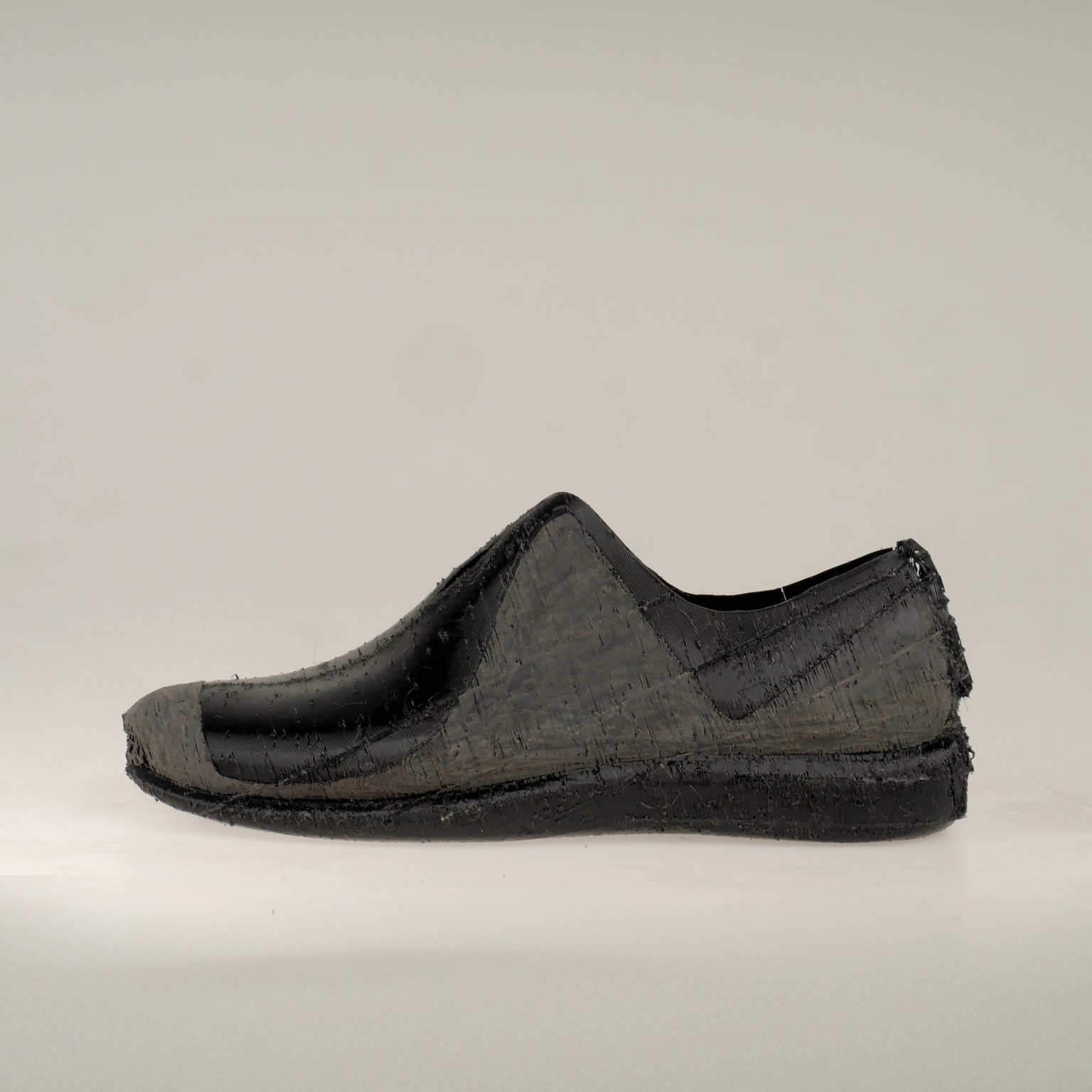
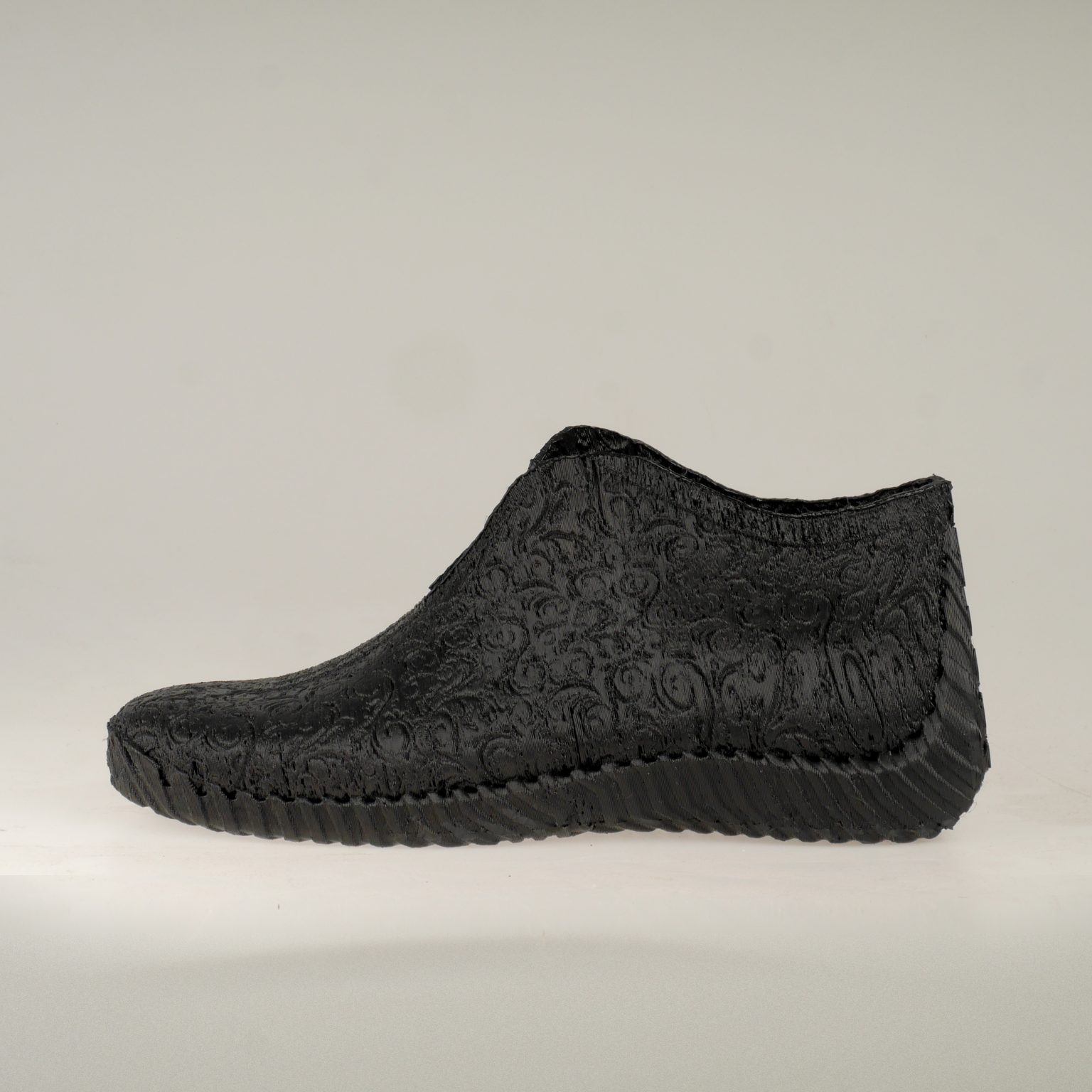
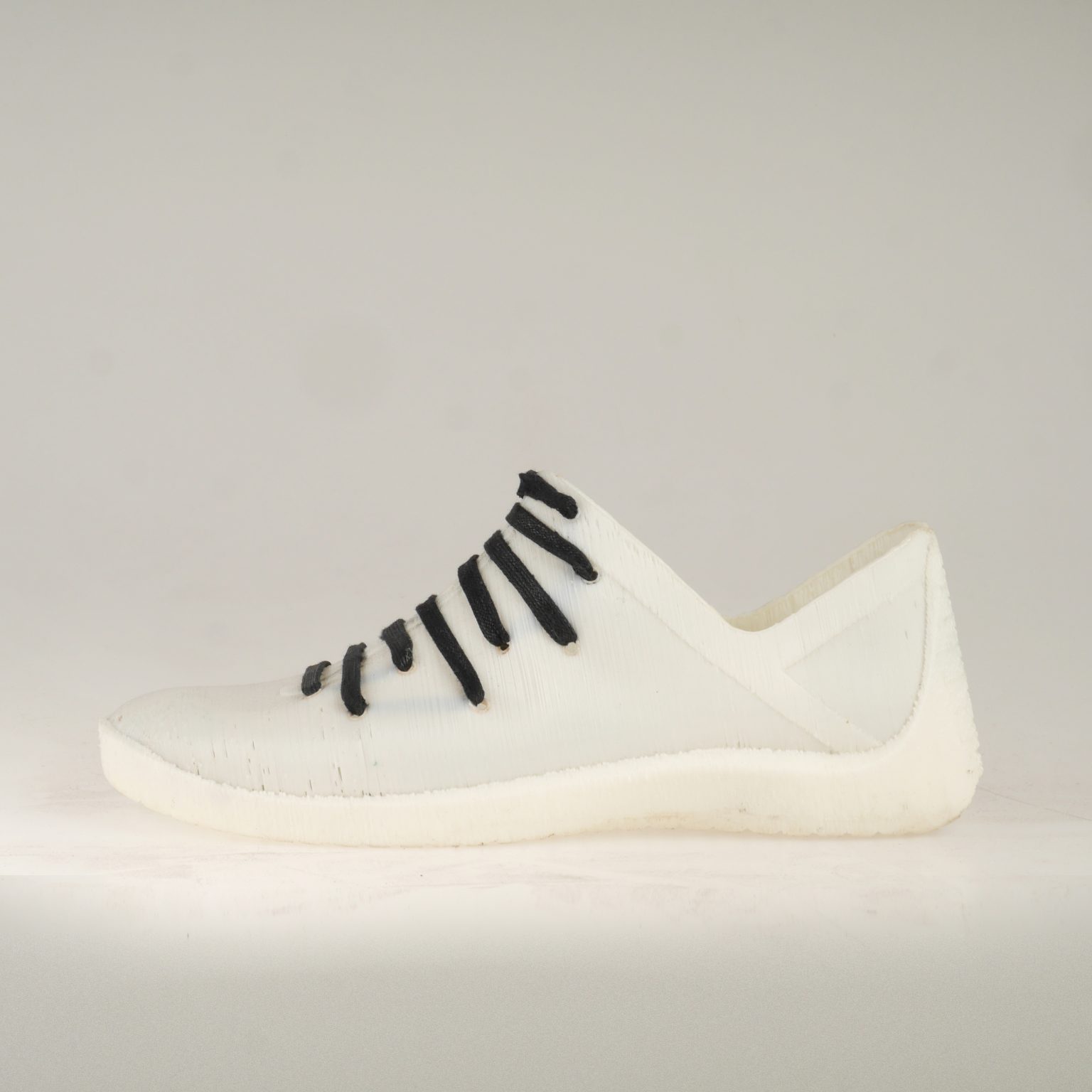
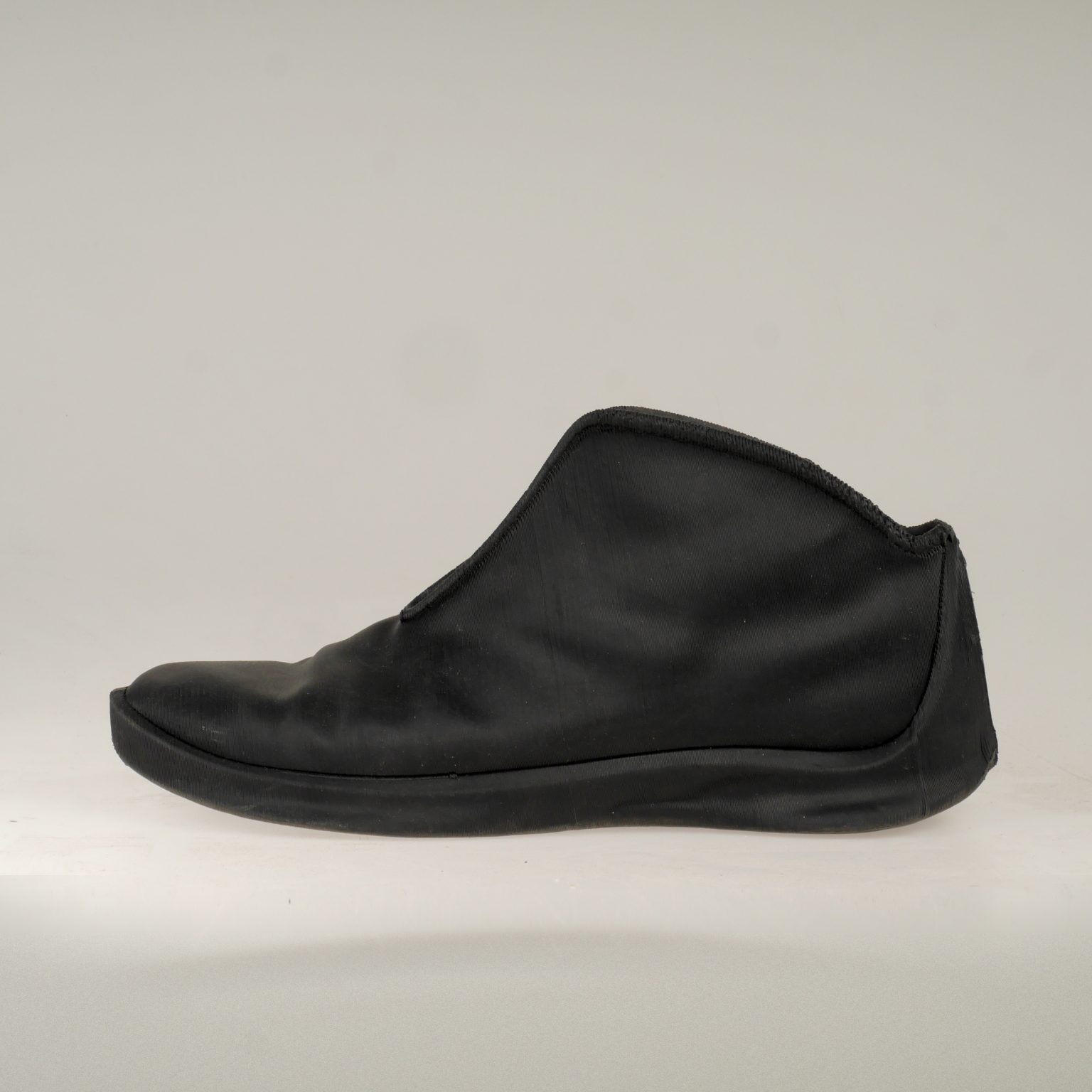
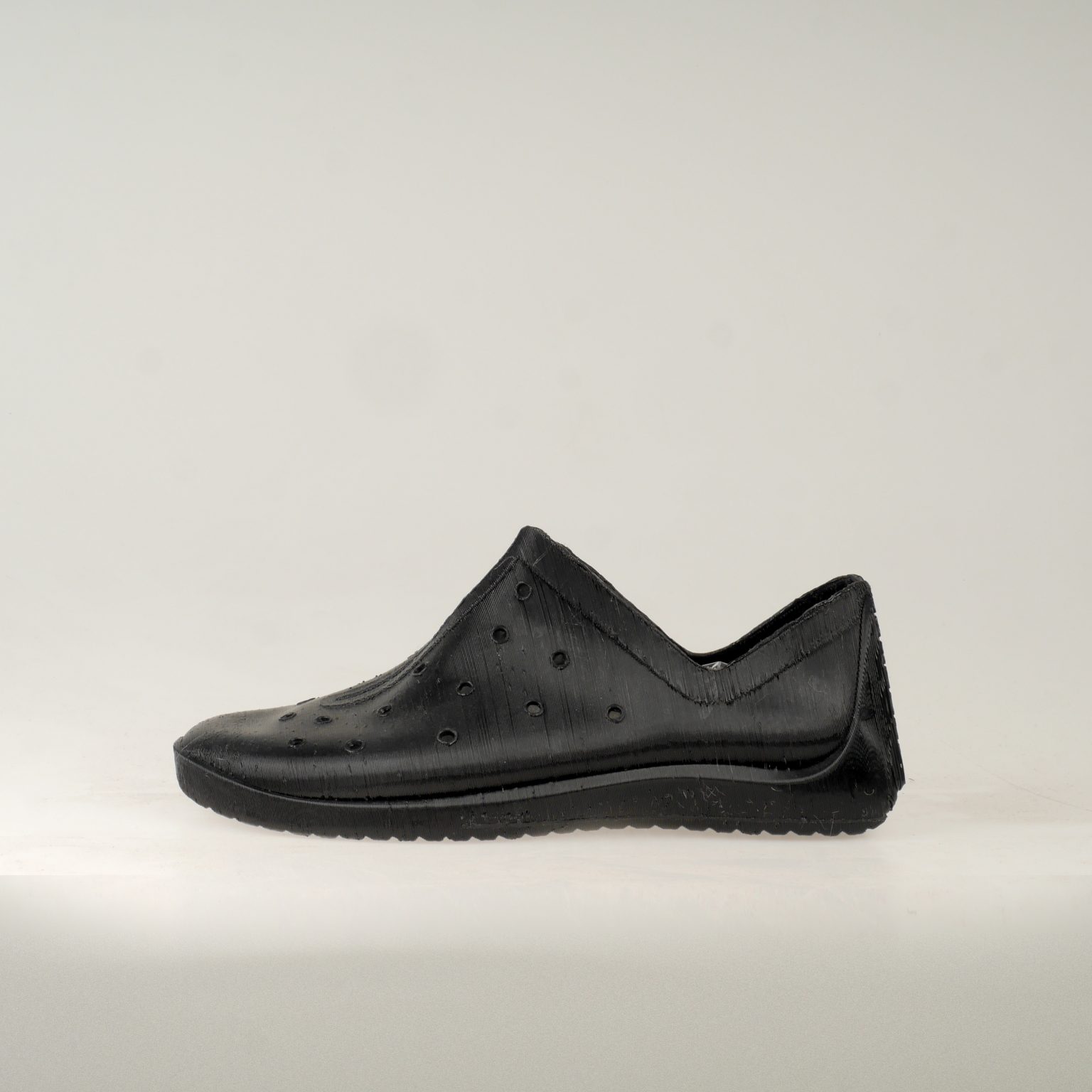
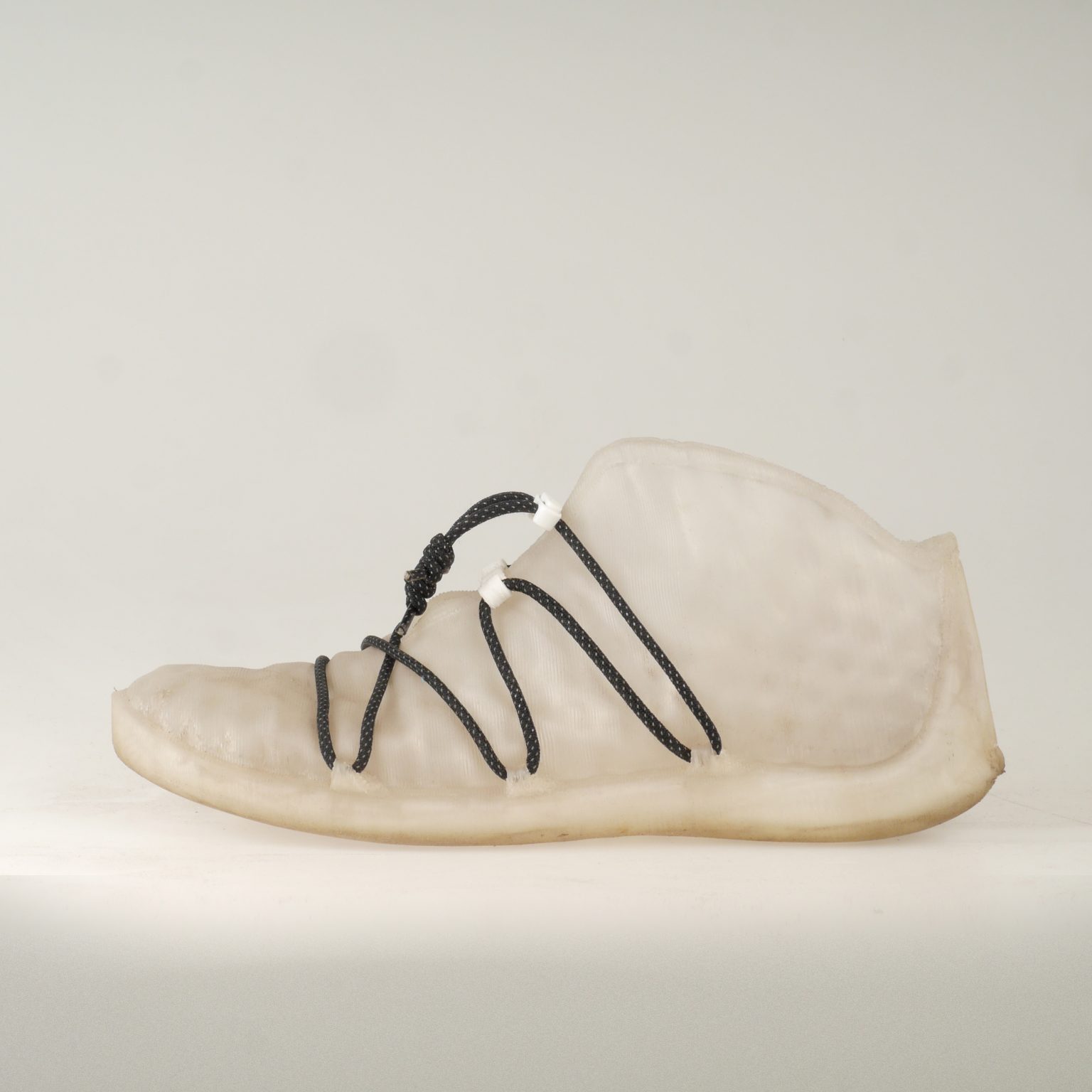
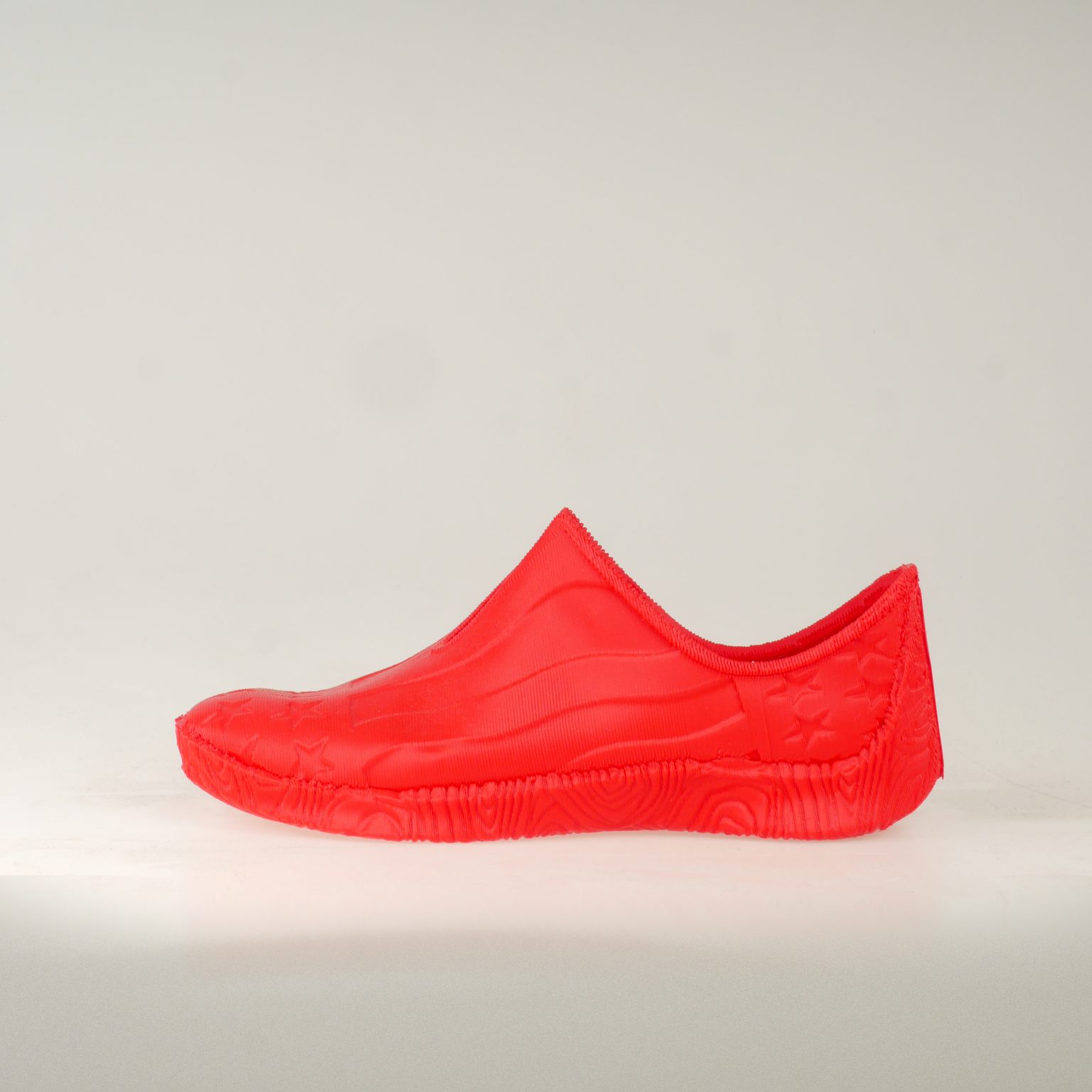
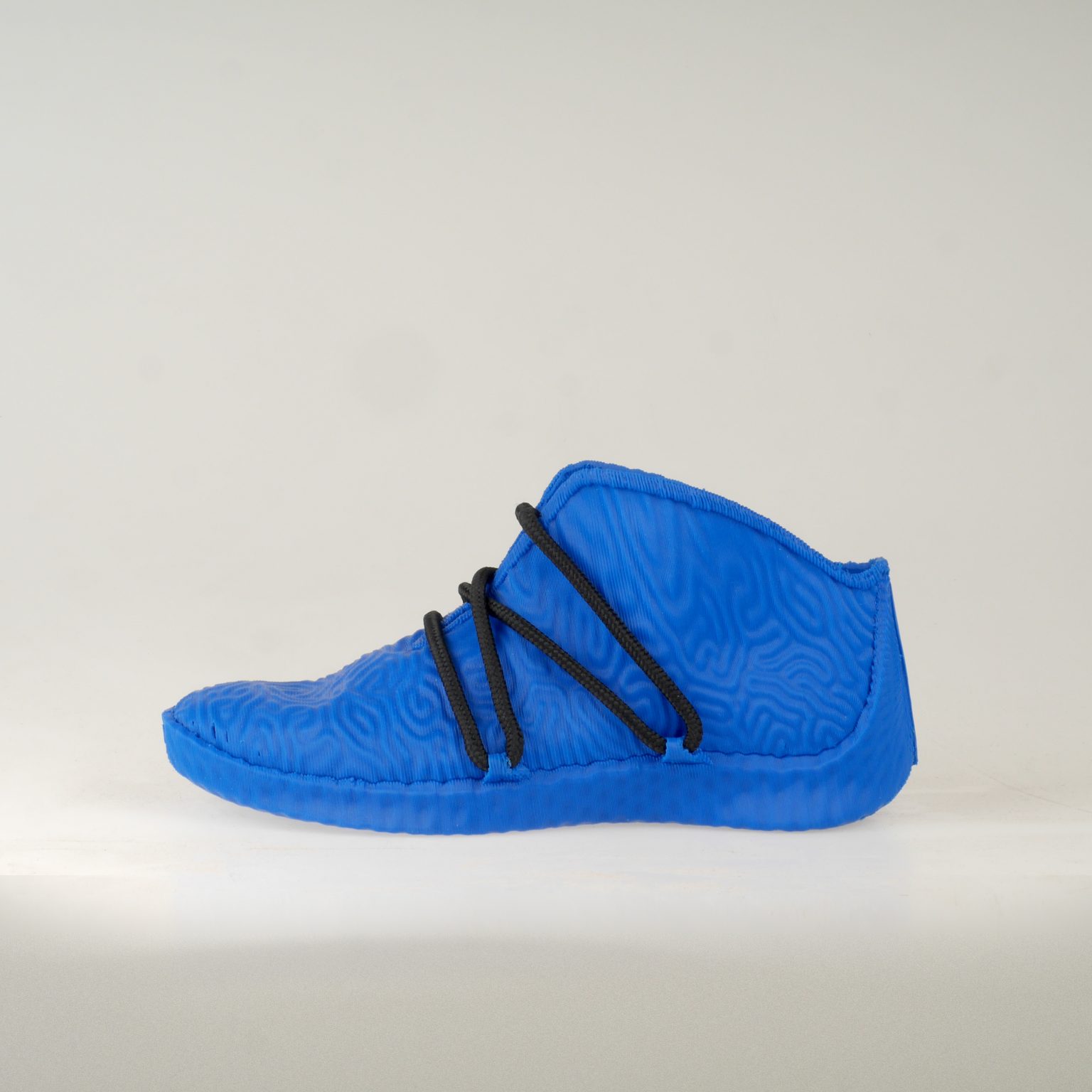
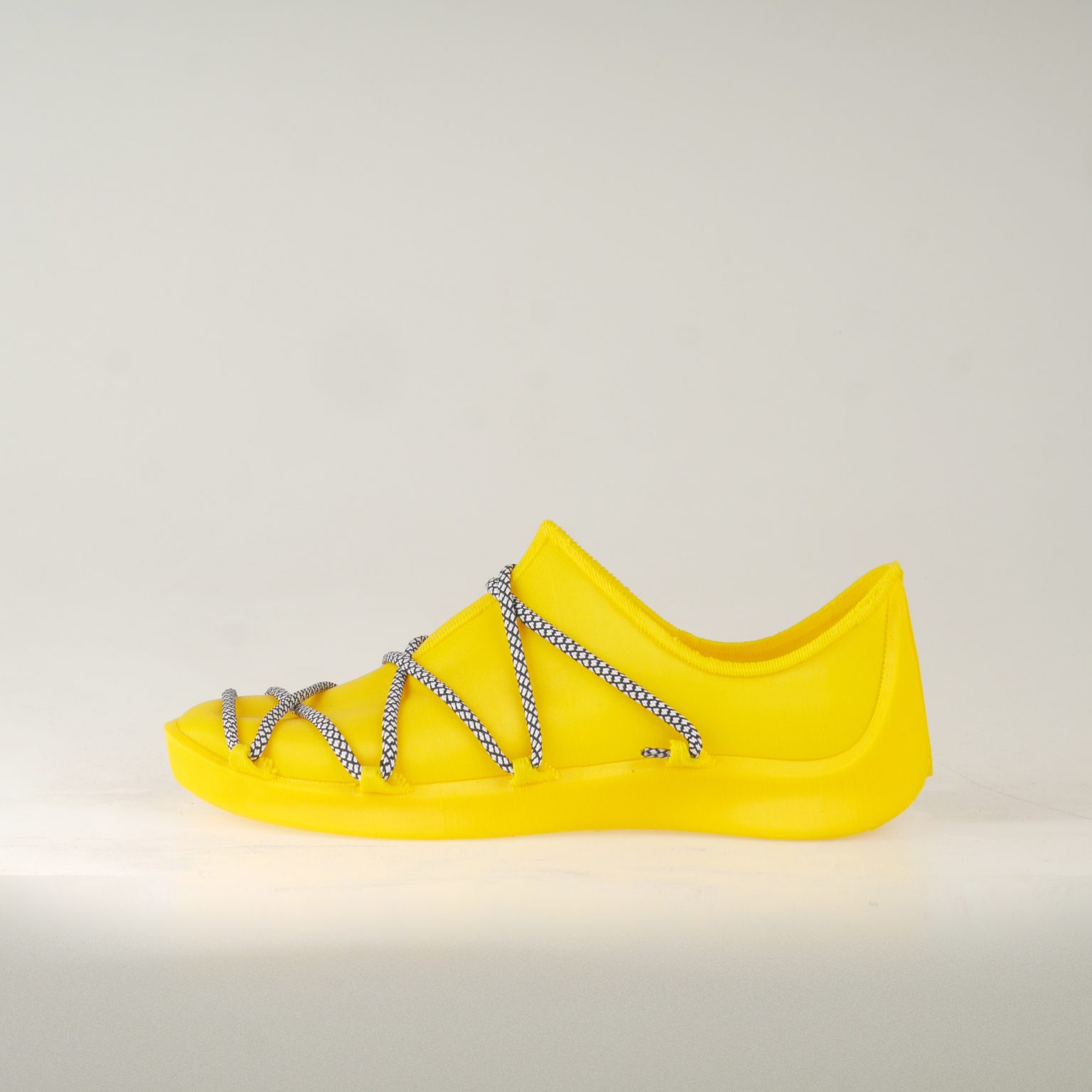
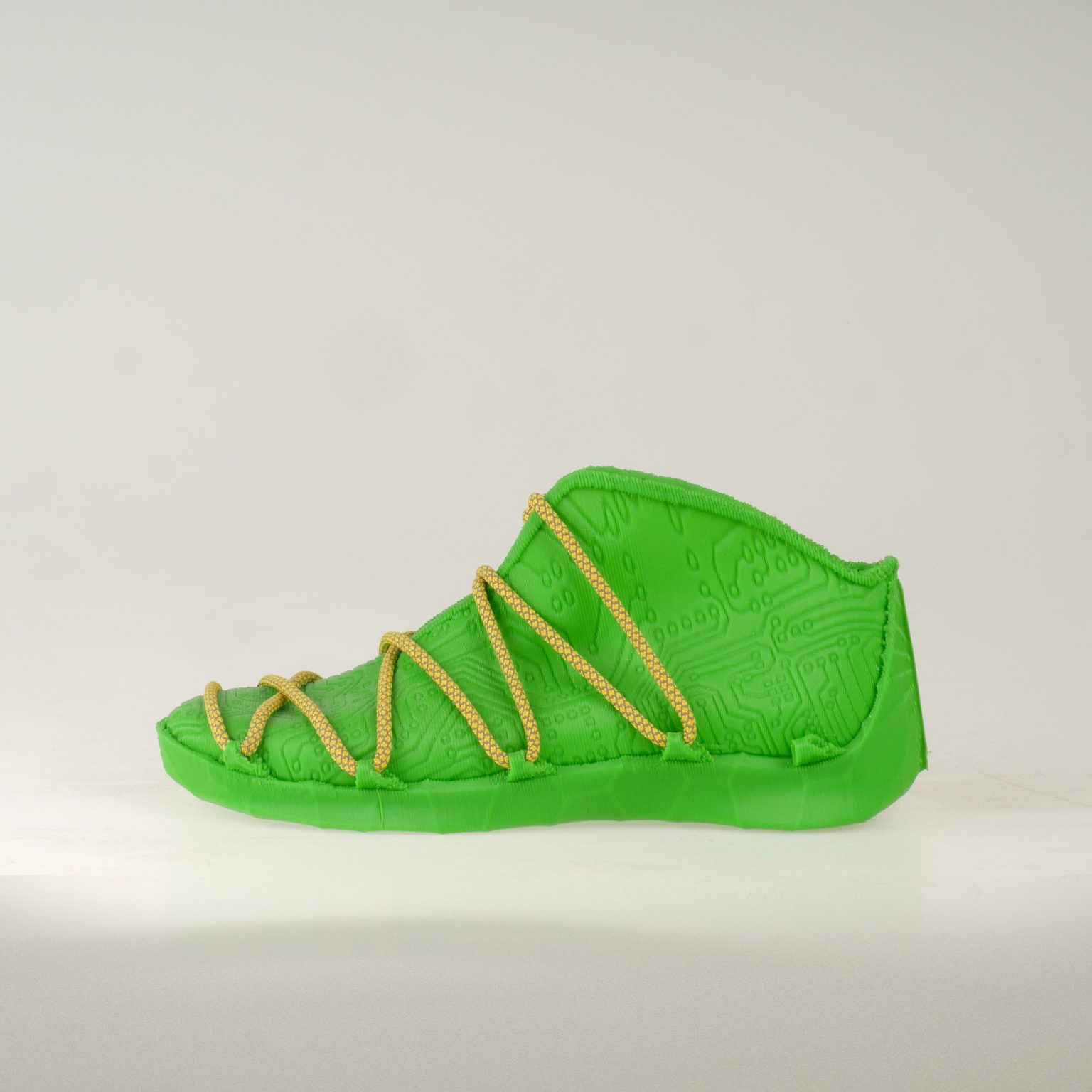
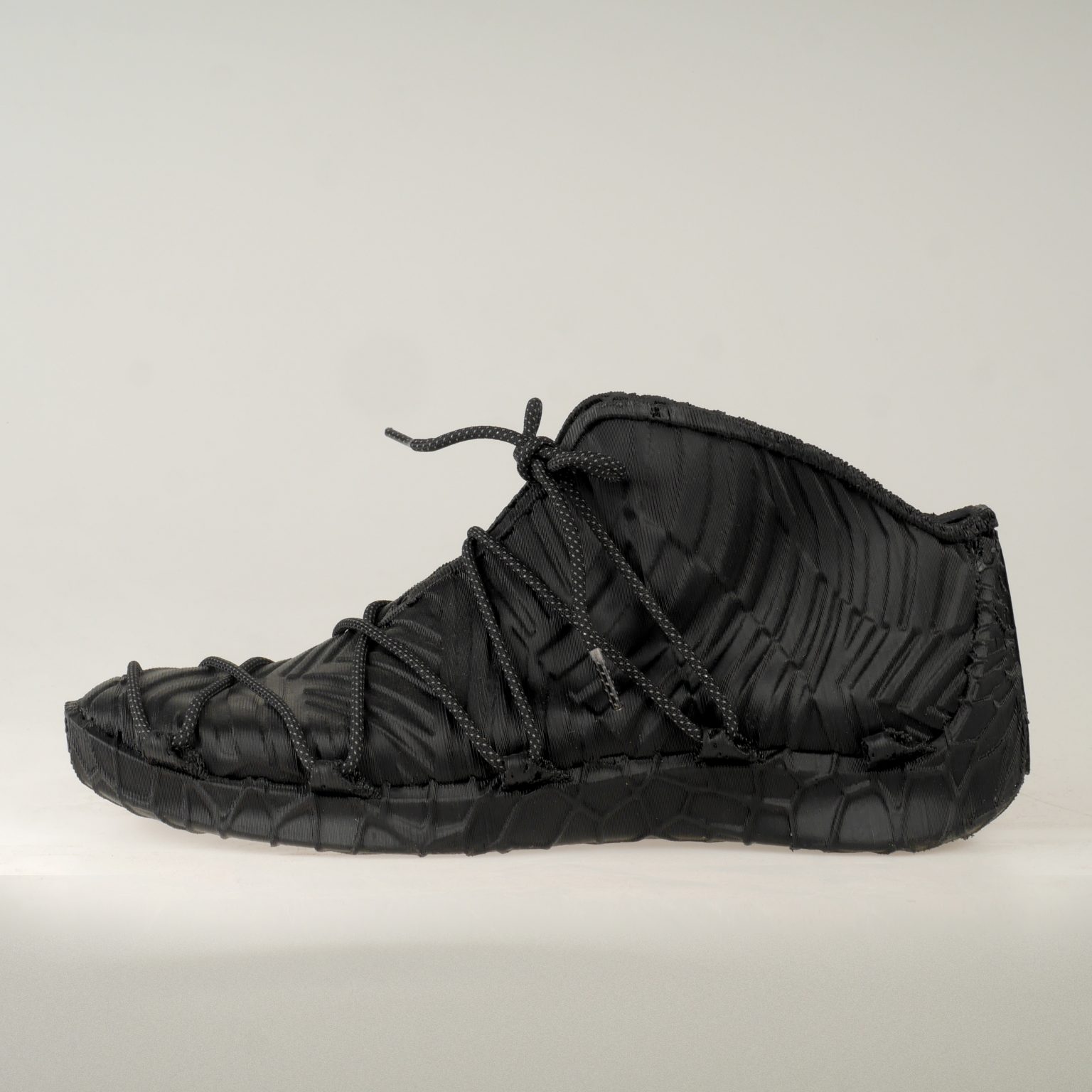

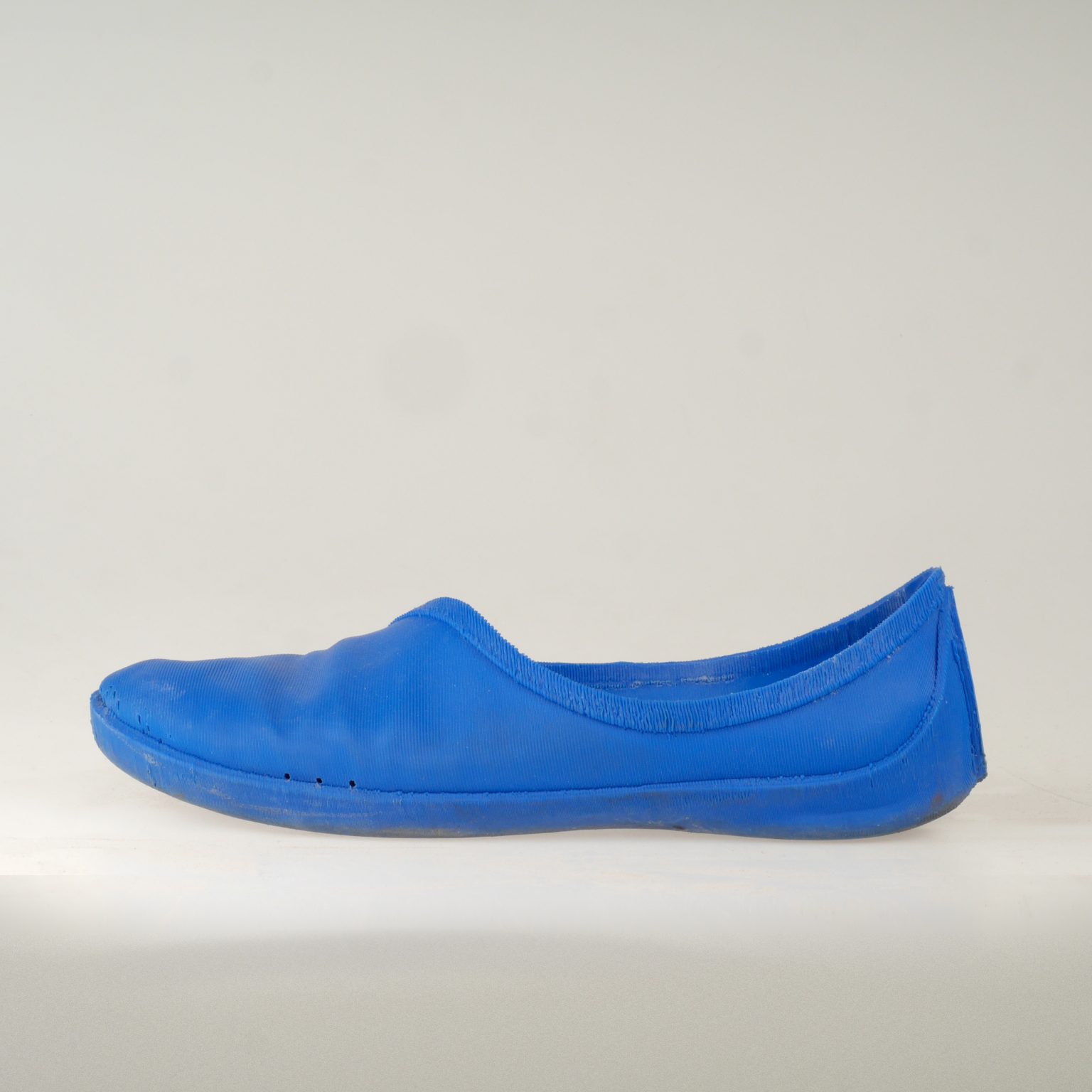
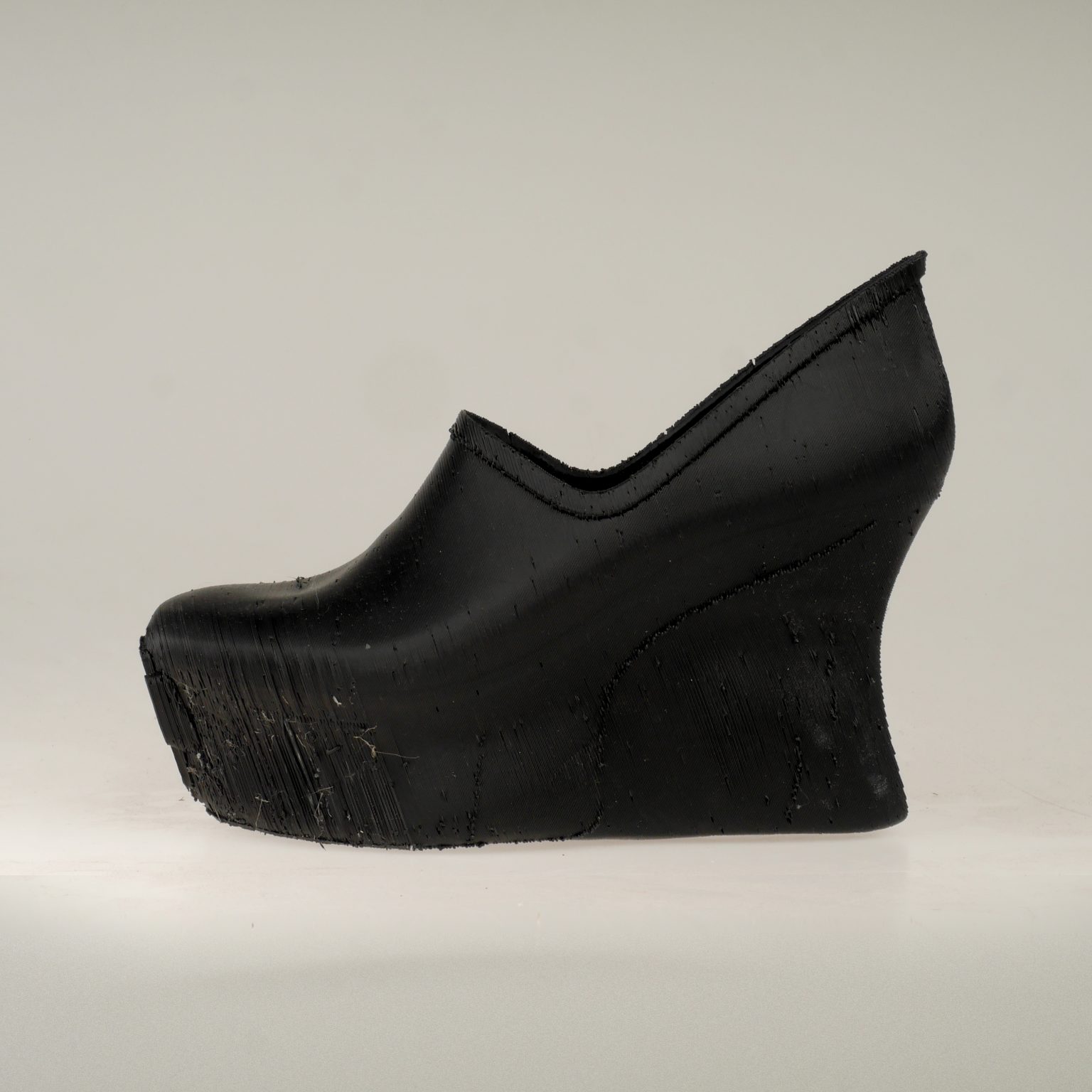
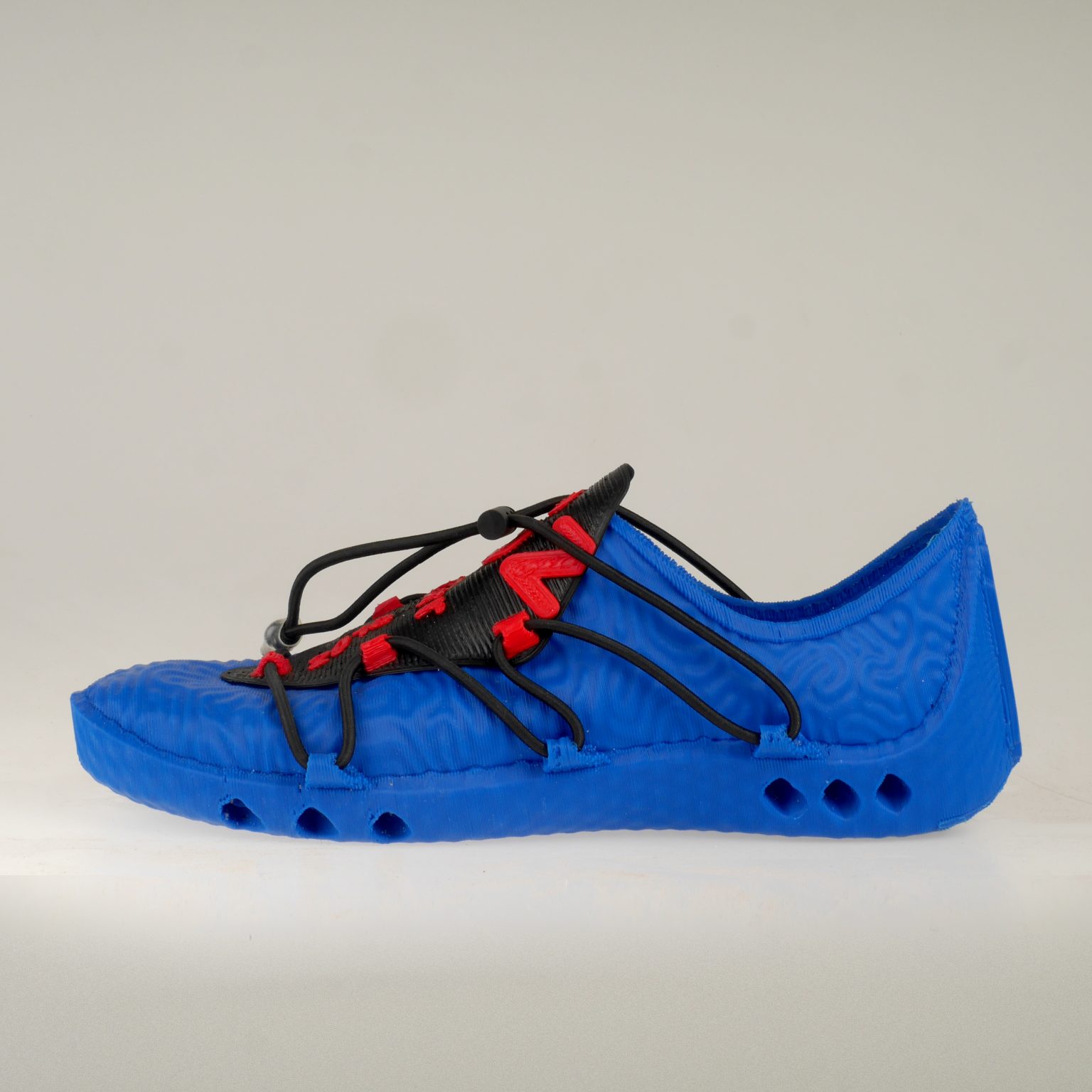
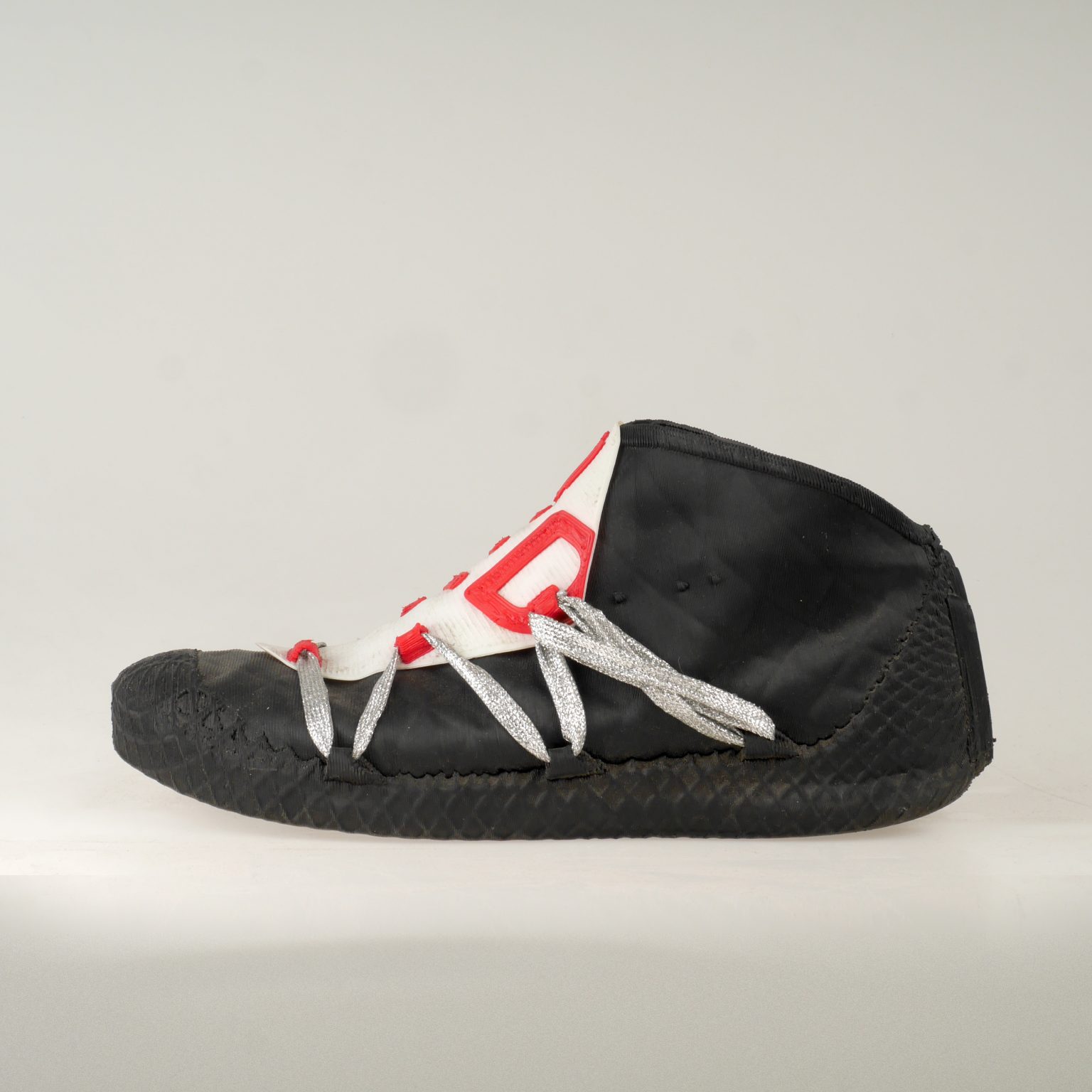
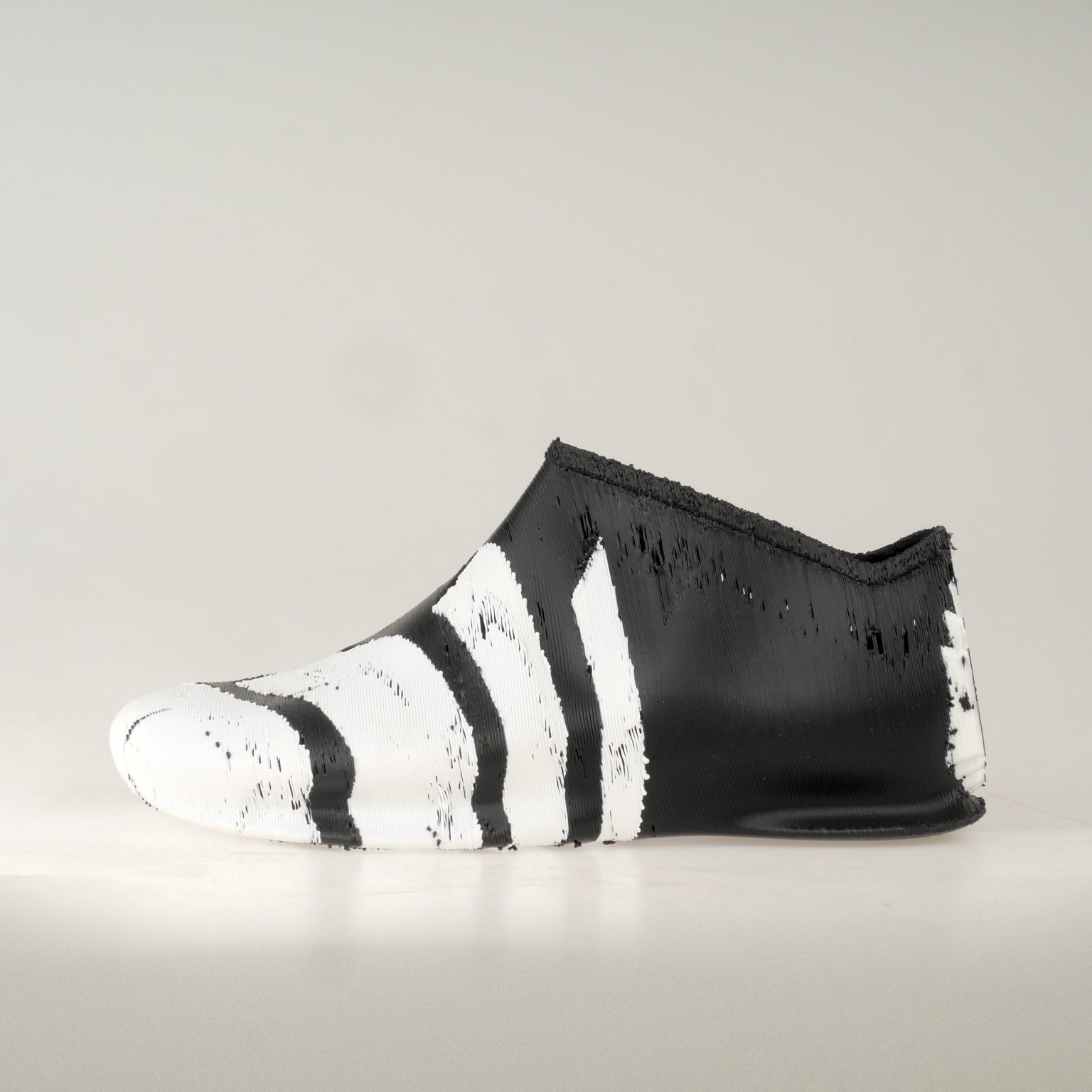
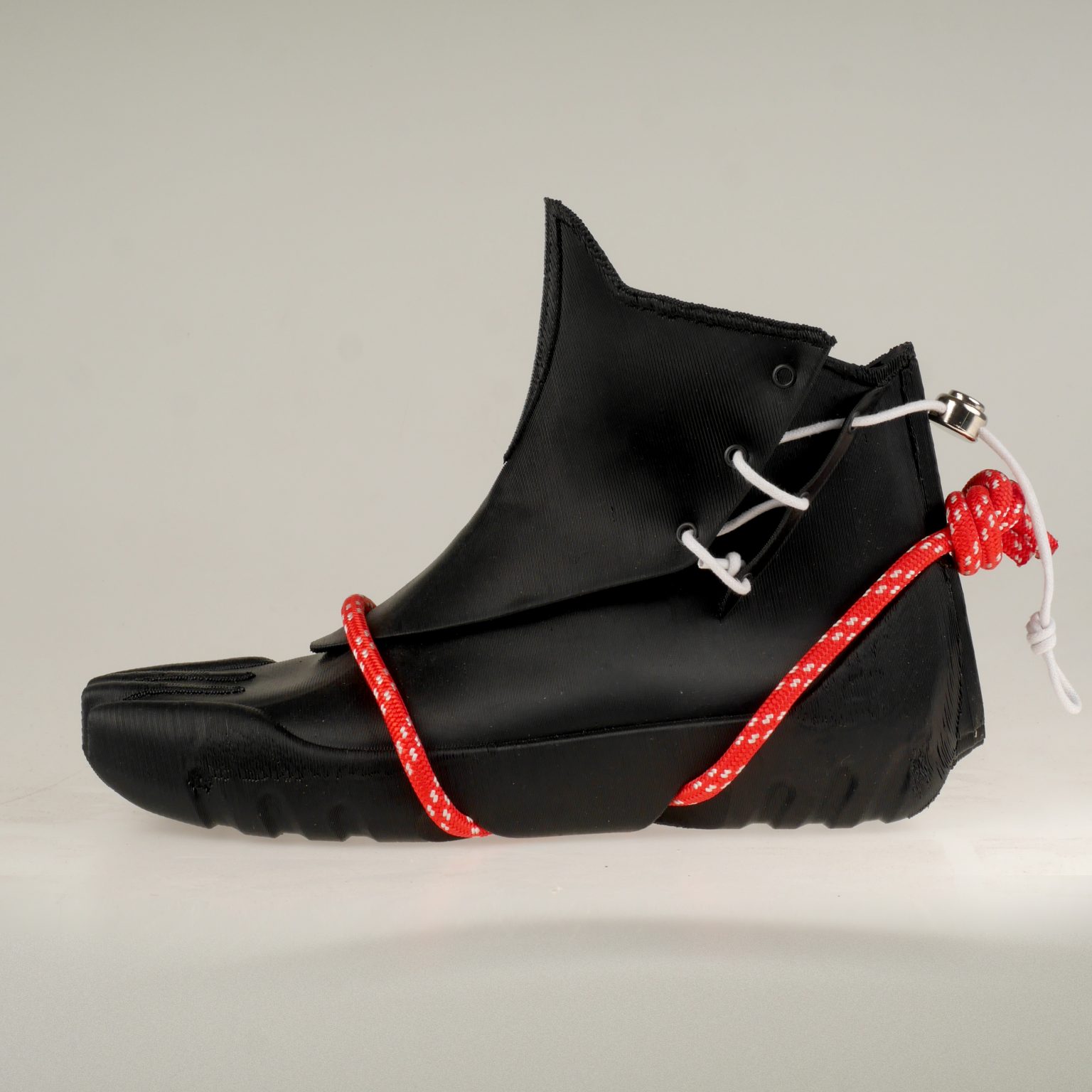
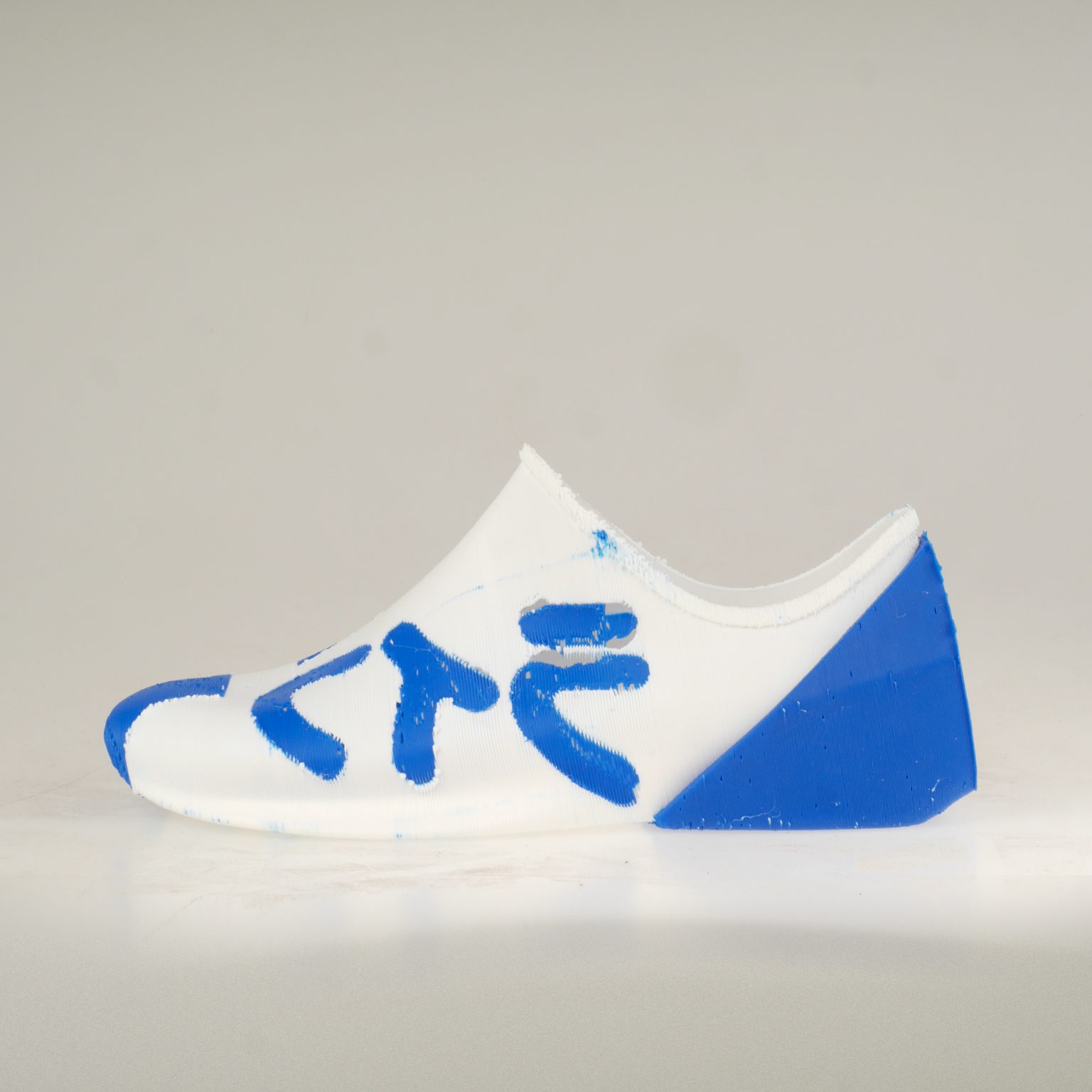
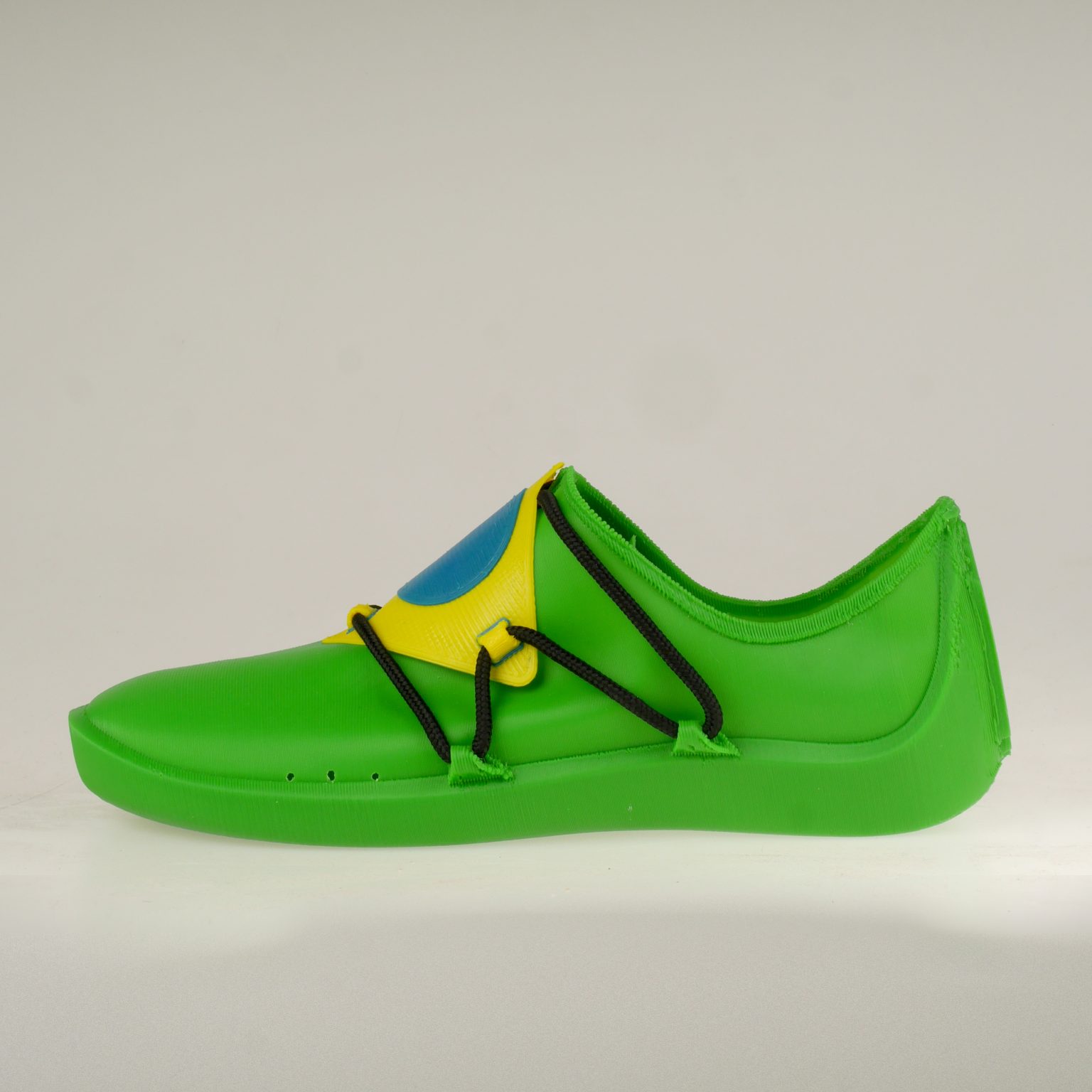
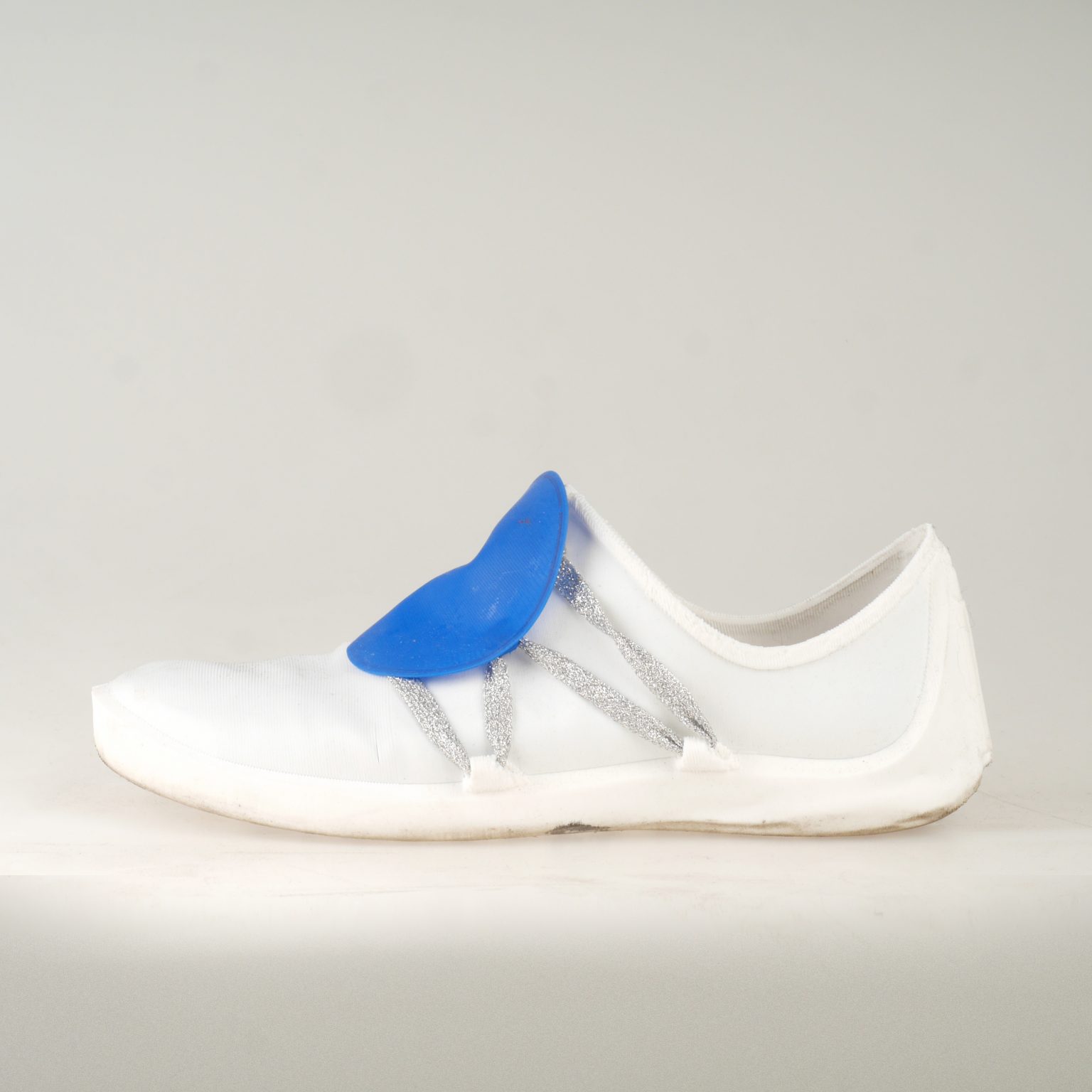
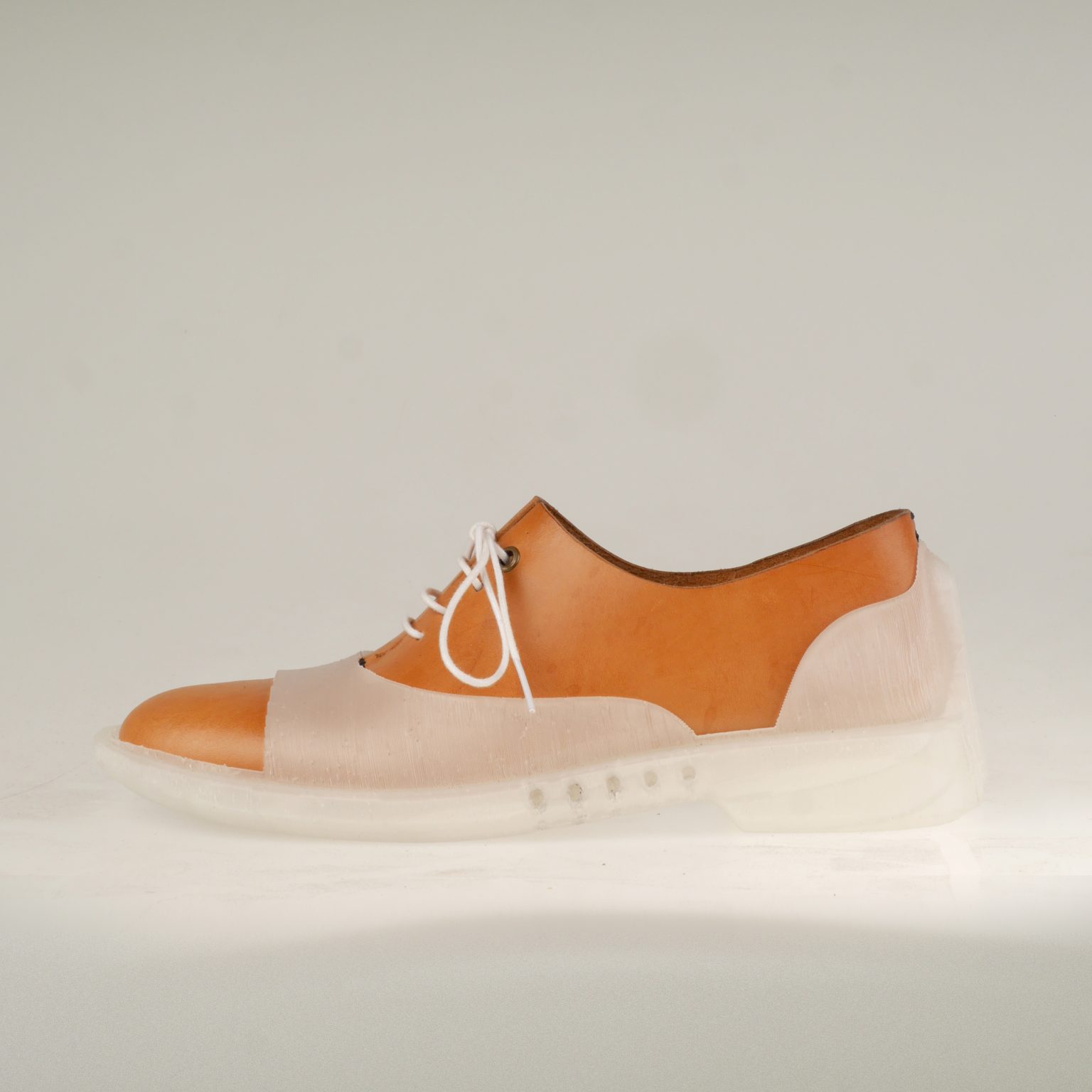
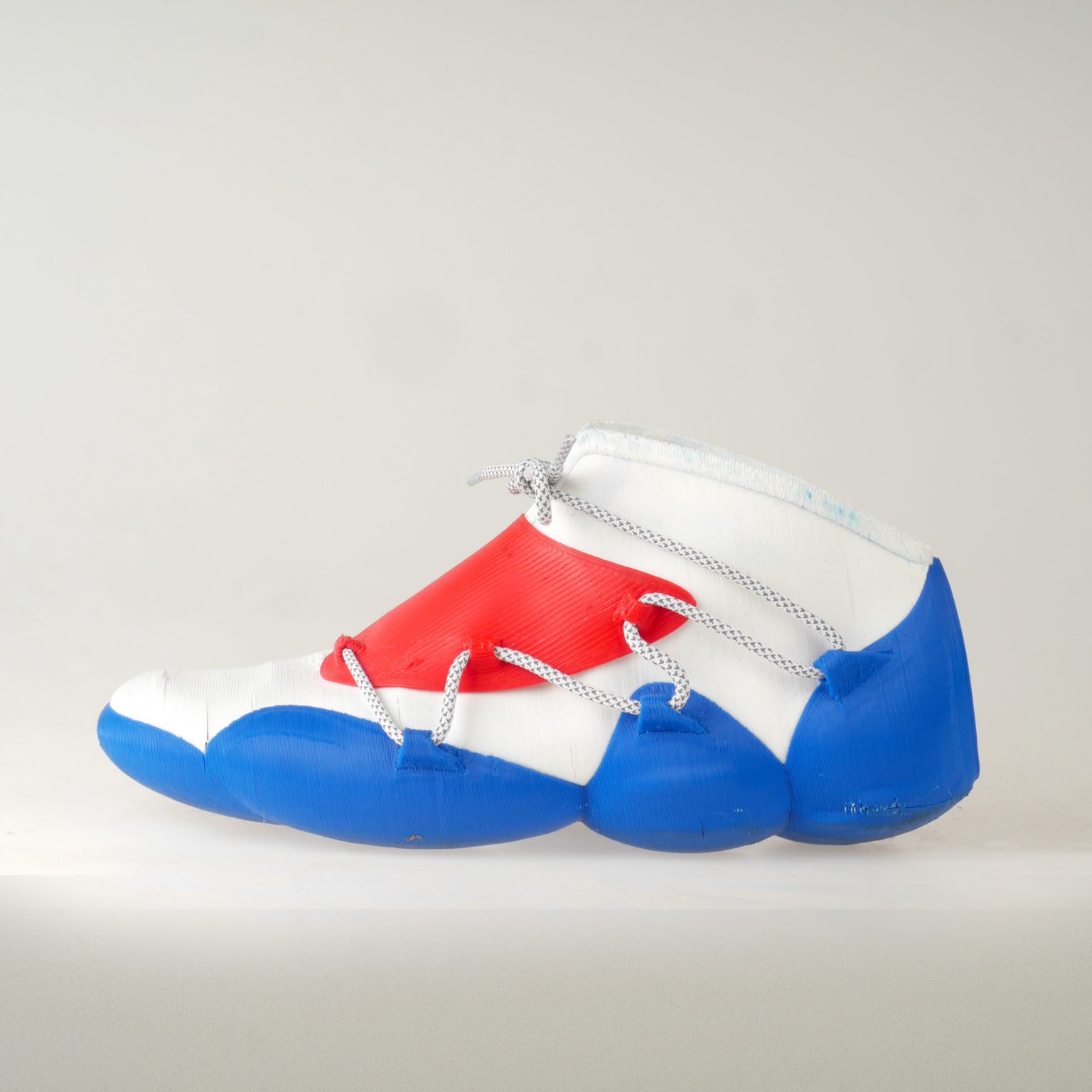
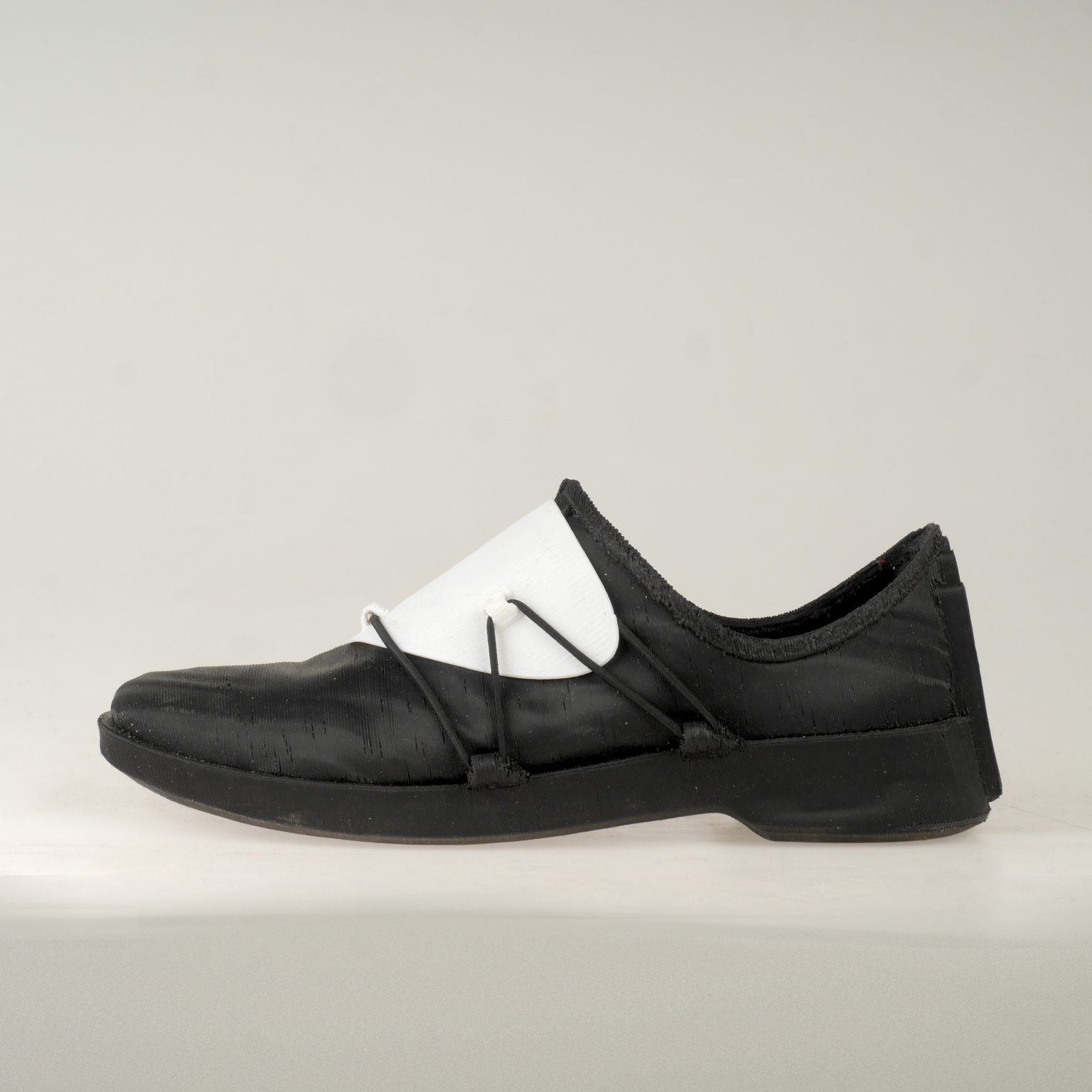
A selection of Philippe’s 2018 designs.
Could you walk me through the evolutionary timeline of all the different iterations of silhouettes and their inspirations?
We’re going back to 2017 (shows early prototype). This is the first somewhat wearable thing I printed that I could put on my foot and confirm the shape. The way I 3D print shoes is through FDM, which is basically just layers of plastic that get stacked. And because there’s not that much flexible materials that are available, most of it is hard plastic, so not particularly good for shoes. And as for the flexible materials that are available, they tend not to bond very well to each other, so this was an interesting test.
The ridges you see on the side are from walls needed for stability that I then cut off, but I could put this on my feet and I could see that it worked. The next thing that evolved into was another shoe where the shape was quite similar, but it was something I could wear test.
Philippe talks about some early models and the manufacturing process.
This is still the same material that I use nowadays. I’ve only found one supplier that makes something that I can actually use for wearable shoes because they worked: I did things like go to the beach. I basically wore these for three months every day and they didn’t fall apart. This is where I could decide “okay, I can actually make a product this way.”
In 2018, I was selling shoes and basically all the designs that I had were a variation of this where as a customer, you could choose a texture for the upper and for the outsole even when the whole shoe is 3D printed as one piece.
I also experimented a little bit with womenswear, which is not as easy for me because of the flexible material. The heel is always a little bit soft for a high heel, so we’ll see. I might return there at some point.
Then in 2019, I came back to Hong Kong and decided ”if l’m going to be successful with this, I got to do weird stuff,” (holds up a shoe that looks inspired by Gundam), so the designs that I’m making now — basically everything goes back to my youth.
It’s all the influences I’ve had. It’s the Lego, it’s the anime and the comics that I bought. That’s basically what is pushing me now.
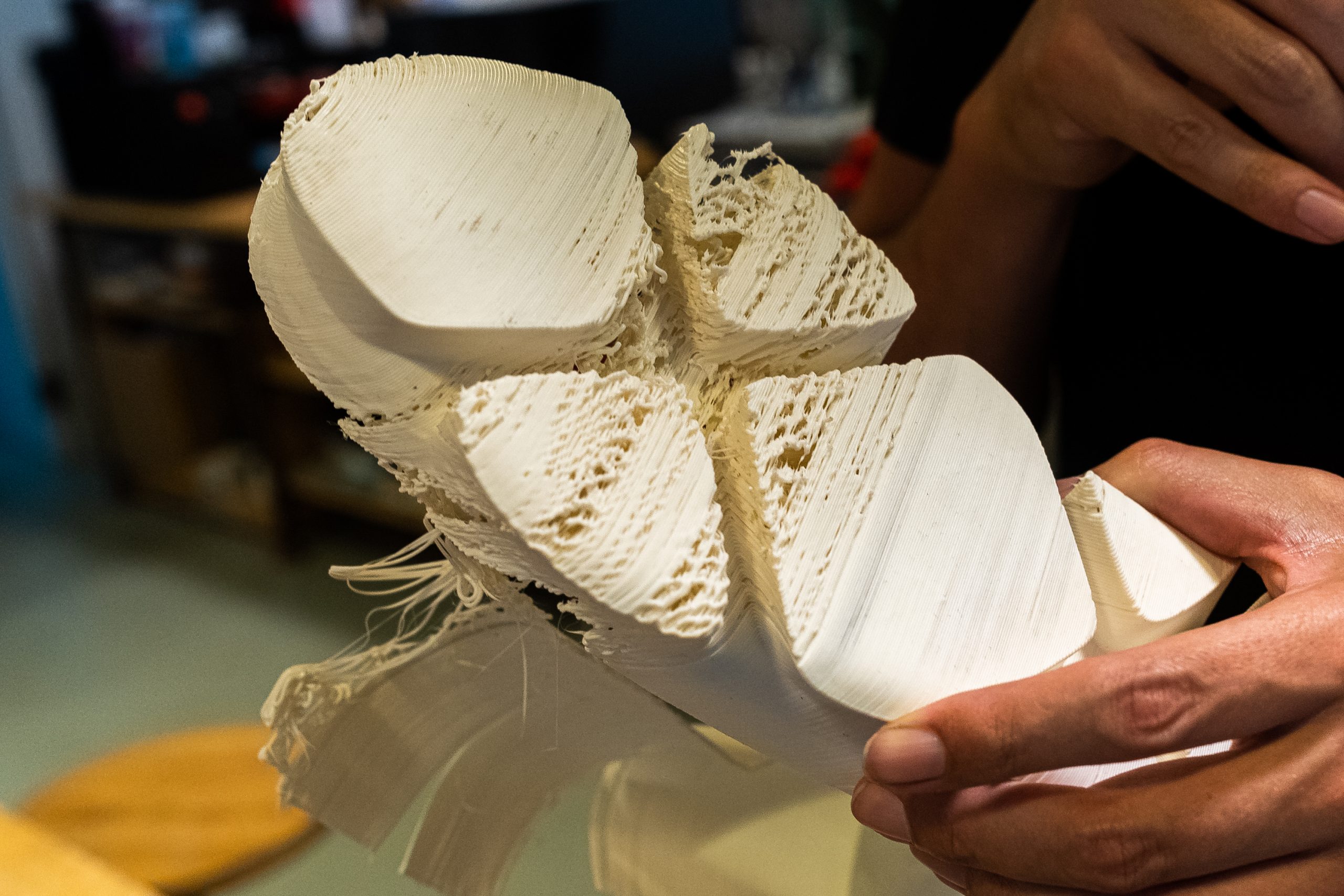
The Process
What steps does it take to design, test and manufacture the shoes?
A well known saying among footwear designers is “last comes first.” And the last in this case, is the foot shape that you use to build the shoe around. So the first thing that I did when I started was find a good last and I found that now, so all my shoes are basically built around the same foot shape.
Starting from that point, it’s actually relatively easy. I don’t sketch enough. Every designer should sketch more, but in the end, I know the reality: We all just dive straight into 3D CAD because we think it’ll be quicker and it sometimes is.
If l have the foot shape, then I can start defining what I want for the shoe. What I’m holding is a weird shoe, but you can basically see what I define as a volume of material that goes outside of and wraps around the last, so you have all these curves here.
You can then define and adjust how narrow the waist of the shoe is, how big or small the outsole is, how close the upper fits to your foot. And after that, you can start working on the surface itself where you can start working on the texture, add panels or you can think about lacing, for example. That’s how the basic process goes and it will be slightly different for every shoe.
Philippe explains “last comes first” and the process of designing a pair of FUSED footwear.
How does one go about picking a last to account for all the variations in foot size and shape?
There is no perfect last! When I came to Hong Kong to start exploring orthopedic shoes, we were exploring the idea of “can you actually make a shoe based on a foot scan?” And even that is difficult because a shoe flexes around a foot when you’re moving and that means that if you would make a shoe that exactly follows your foot, it wouldn’t be comfortable because there wouldn’t be enough space for the material to flex.
Luckily, I have a relatively neutral foot, so when I started this, I basically made it around my own shoes. Since then, I’ve now found through both the shoes that I’ve sold and the lack of complaints that I received, I know it works for most feet.
But I’m also not doing custom shoes, but standardized with a slightly weird sizing system that I had to figure out. On that note, even just regular shoe sizing is weird.
If you always wear Nikes and you know your size, even if you order a new model in the same size you always have, it might not fit well. So there is no universal system for sizing except for foot length. that’s what my sizing system is based on: five millimeter increments, as used in Japan and Korea. And then that’s been translated back to your UK, European and US sizes.
3D printing a FUSED sneaker via Fused deposition modeling (FDM), which involves countless layers of hardwearing Thermoplastic Elastomer (TPE) filament.
The Technology
What software do you use for your designs and how does that compare to other programs where you would model or sculpt your design?
I use Rhino 3D, which is not used as much anymore considering that it’s been a while since I finished my studies.
In 3D software, you have a couple of different directions. You have the NURBS, (Non-Uniform Rational B-Splines) modeling direction that basically means everything starts with a line whose shape is defined by connecting dots. Then you take multiple lines and you define a volume in 3D space and by creating a surface between those lines.
Rhino is definitely modeling. It’s used a lot in the shipping industry for boat hulls and stuff like that because it’s good for modelling organic surfaces, which programs like Fusion 360 or SOLIDWORKS are not particularly good at. Those programs are great for the box shapes that you put your electronics in, but as soon as you want something curvier, then you’ll go to Rhino, for example.
I also think that the CAD programs kind of form your aesthetics and the style that you’re able to do. I’m very comfortable in Rhino and if you have a 3D CAD background, I think you might also be able to tell that from what I designed.

A cross-section revealing the plastic filament lattice inside “solid” parts of the shoe.
Are there other approaches as well?
You also have polygonal modeling and that comes mostly from the animation background. That’s where you have a blob that’s made up of thousands of tiny little triangles called a polygon mesh and you can start pushing those triangles and pulling them and then sculpting them (with programs like ZBrush).
It tends to lack the dimensional accuracy you need for product development or for anything that needs to be very precise. As soon as you want to do mass production, then you’ll need to start work with all the different programs.
That said, I think modeling with meshes is going to be the dominant future 3D modeling stream, mostly because it gives you more freedom. I actually need to learn Blender because it’s such a great mix of different styles. You can do almost anything in Blender, which is very cool.
Also very cool is Gravity Sketch, a virtual reality program. If you have Oculus goggles, then you can put them on and design in 3D. What I see on Instagram with the younger designers is they’re jumping on it because it’s so much easier for them to actually work in 3D that way.
They just pick it up and they come up with great concepts. Although they probably cannot be directly made into a shoe, but as sketches, they’re awesome.
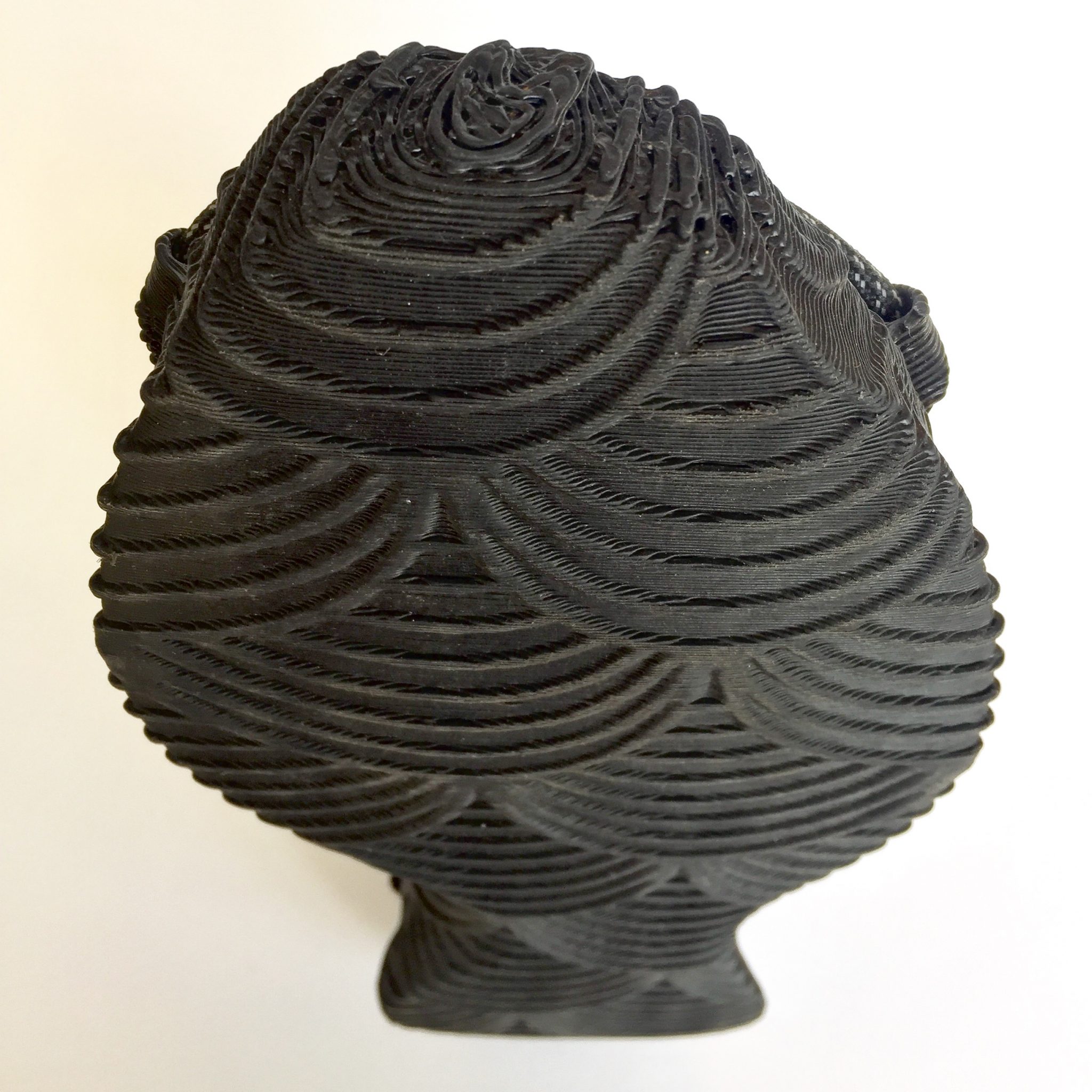
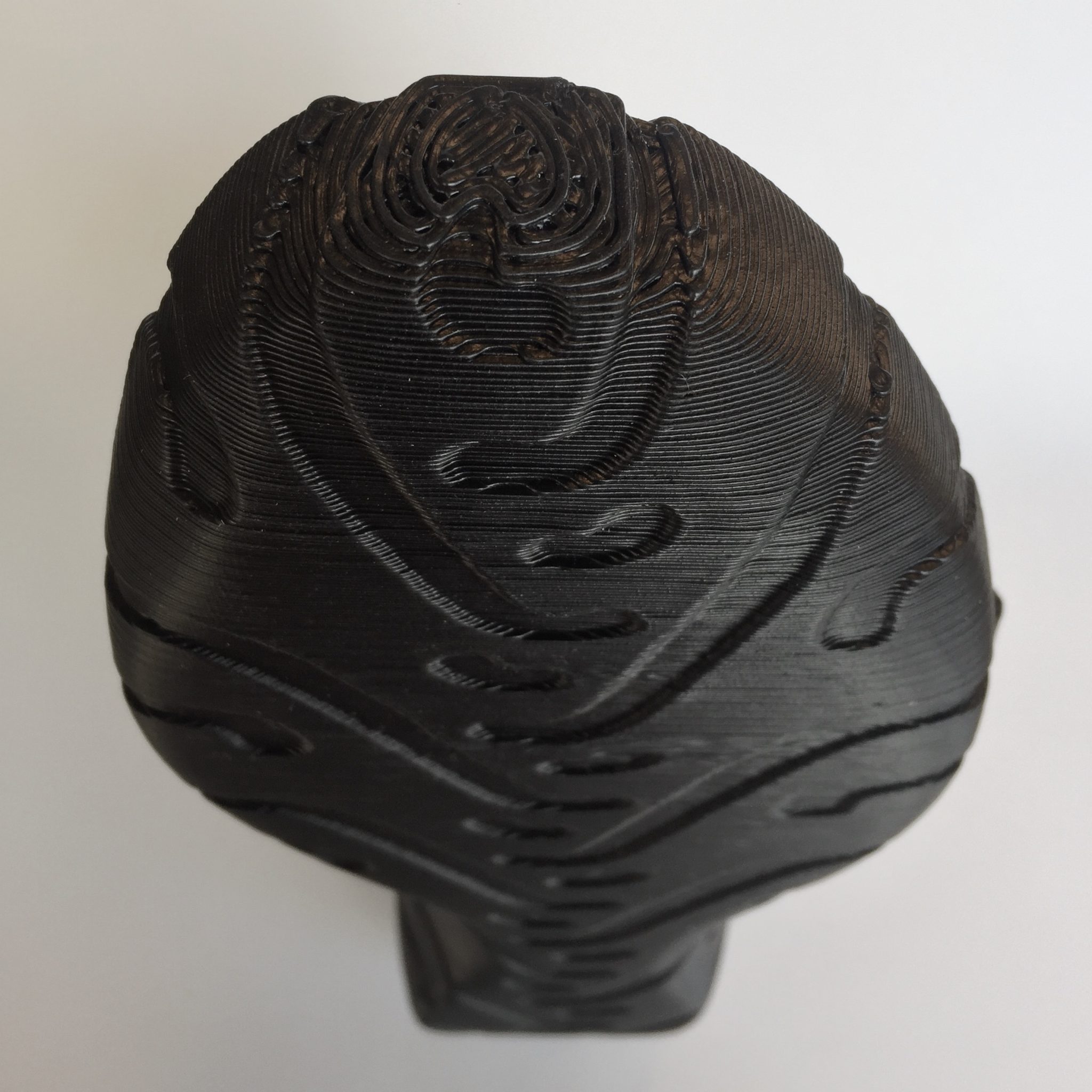
Given your experience with the evolution of both software and hardware, what aspect of your process wasn’t possible until now?
Five to 10 years ago, 3D printers just weren’t advanced enough. I think 3D printing has developed and there’s been a lot of refinement, but I’m still not using the high-end stuff. What I’m using now is basically what I had five years ago.
It’s kind of like the first time you had MacPaint and you were making images on a canvas that was 1024 x 768. Now, when you’re sketching on your iPad, you’re actually working on an image that’s 4,000 x 3000 pixels, so it’s much more refined.
I’m still using the MacPaint, so to speak. I print very rough and that allows me to do it at a very good price, but that’s also why you don’t see much 3D printed footwear yet on the market because it’s expensive to create the level of detail that we are used to from all our other products.
What materials do FUSED shoes use and how are they different?
With FDM (Fused Deposition Modeling) 3D printing, there’s two types of flexible material: there’s TPUs, which are Thermoplastic polyurethanes, and there’s TPEs, which are thermoplastic elastomers.
I use TPE through the one supplier I found that is so far the only material I’ve found that can withstand that stress. If you have a shoe and it flexes, there’s a lot of stress happening on all of those layers.
The fact that it’s all one material and that it’s a thermo-plastic means you can grind the shoes down, melt the nibs and you can make something else from that material. We’ve only sold 60 pairs or thus far, so I’m not doing that yet, but that’s the dream.
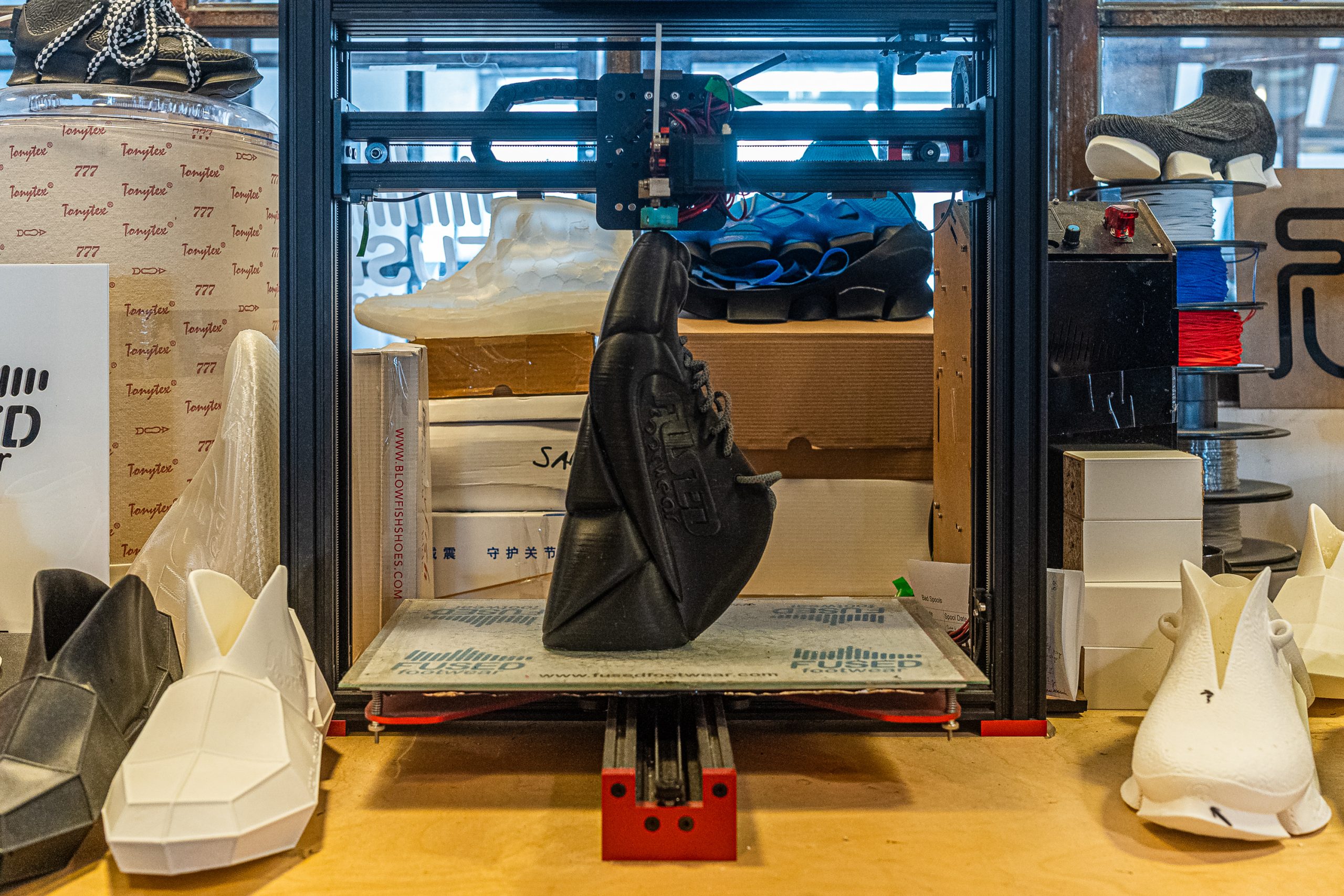
The Business
What’s it like being a completely one-man operation?
It’s both tough and fun. I’m sure it’s not for everyone, but for me, it’s been very good so far. I’m still not good at business and I wish I had more of an education in it, but most of us learn how to do business while living through life.
FUSED Footwear is a passion project that I’m now trying to make into a business or brand, but I still have a lot to learn. I can do the basic stuff like buy my supplies and figure out what price I should ask for my shoes, but I have no idea how to scale this. I have no idea if l would want to take out a loan and probably don’t because I don’t really believe in the whole credit system where people take out loans and then they’re stuck with that. It’s a scary thing if anything goes wrong, so I’m not ready for that.
Is FUSED a business for you?
I’m still working part-time (which is close to full-time), but with just enough time to do the shoes, but hopefully at some point, I’ll have enough sales that this will be my main income. Then I can start hiring people slowly and figure that stuff out because hiring people is also going to be very interesting, but also a whole different level of responsibility.
The difficulty after that is the amount of time that you have, especially at the beginning, when these projects don’t make money, you need to balance all of that, so it goes a lot slower.
Still, I would always advise anybody to go for it if possible if they can find a way because you get a lot of personal contentment from it. I have some friends here at Maker Hive (the co-working space where Philippe is based) who create custom keyboards and printed cups and it was the same case; you’re really growing as a person because you’re doing something that you love. If you’re stuck in a job — maybe even a job you like — you’ll still get a lot more pleasure from doing a passion project, which is why I think I’m okay with doing it alone so far.
For now, I’m just trying to grow it slowly, and hopefully, that’ll also give me enough time to learn those skills while I’m doing them as I’ve done now for four or five years. Thankfully, I’ve been able to do it at my own pace and without any of those “scary moments” because I haven’t invested all of my life in it.
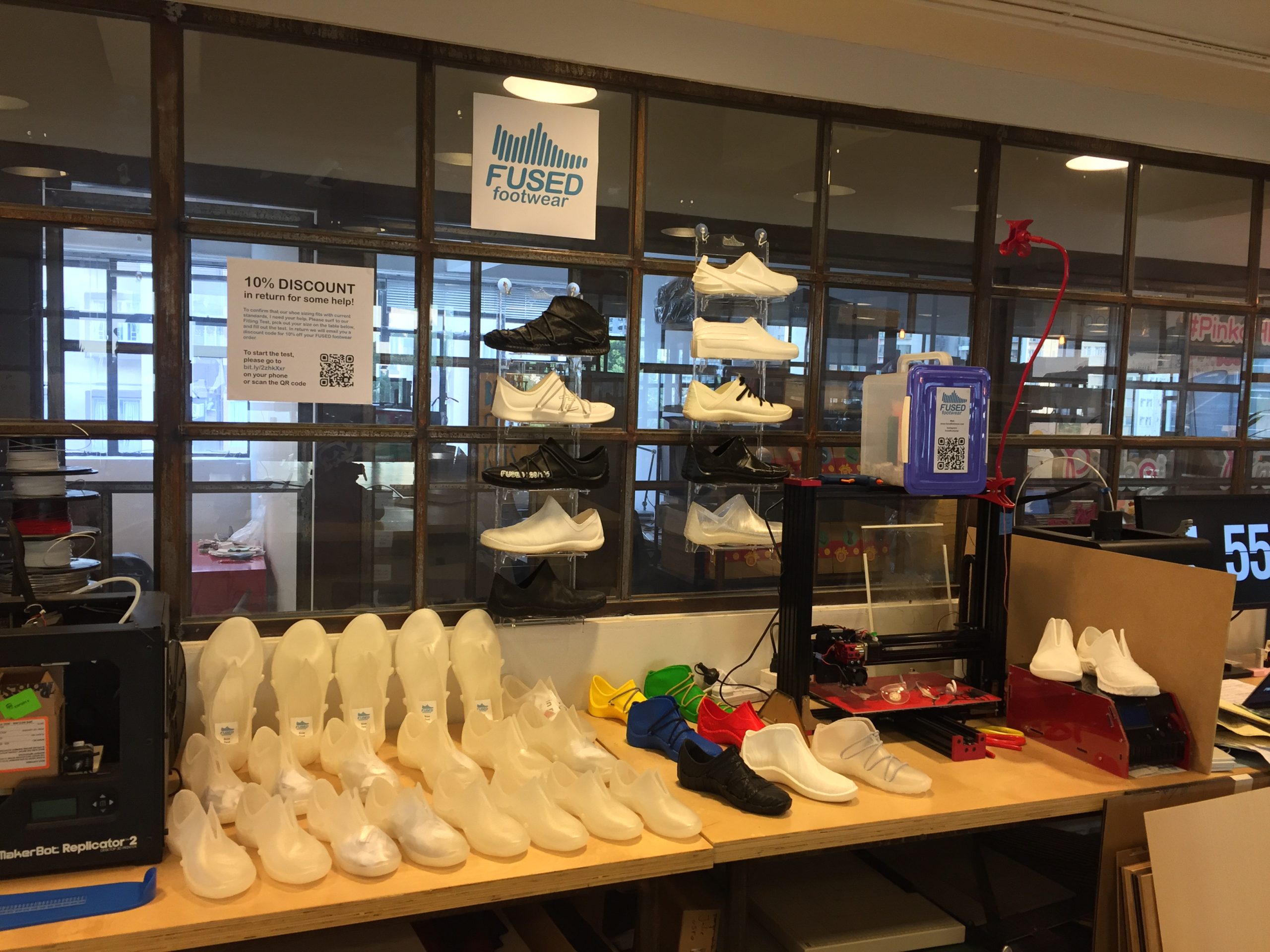
A 2018 shot of Philippe’s work area he took at Maker Hive in Hong Kong’s Kennedy Town area.
Because it intersects hands-on education, creativity and business, could you talk a bit about how that ecosystem has been like in Hong Kong versus say, Holland?
Hong Kong doesn’t have very high taxes, which everybody loves, but it also means that Hong Kong doesn’t necessarily have a lot of money to spend. Things like the arts and the psychological comfort of doing a hobby are not “niceties”; they’re essential for society and I think that is somewhat missing in Hong Kong.
In Holland, there is a lot of creative industry, great schools and a social safety net that allows some people to just do different stuff if they want. Having that in a society is so inspirational for older people who are a little bit higher up the ladder, or are a little bit closer to actual client work. I really miss that here.
I think the funny thing is that Hong Kong has great arts education: there’s design, photography, film, and graphic stuff. Everything is here. The schools are good and the teachers are super good, but then when those kids come out of school, they don’t actually have that many options. And that is, I think, very sad. Many people still live with their parents until they’re 35 because it’s so expensive to live here. I imagine that’s part of the problem as well, but how do you fix that?
An example here is I know of at least four or five different companies that came out of this makerspace just because here they had the tools to develop what they want, or they could find a space to have a workbench to put their machine on it to start making stuff.
Having been here at Maker Hive for a bit over five years, I came originally because I needed a 3D printer and that’s what they offered here. The fact that in Hong Kong, where almost nobody has their own workshop and it’s very rare for people to have their own tools, so because you can come here and make use of both the space and the tools, that’s a great start for somebody who has an idea.
So I think makerspaces can play a big role there in terms of that type of culture. If if a city doesn’t have a makerspace, the cities should find a way to have a makerspace. They don’t have to fully subsidize it, but I think if any city has individuals that want to make stuff with their hands and if they can’t do it at home, what can you provide as a city to do that?
On the topic of schools, with all the technology that’s available now, is that formal education route still super necessary to do something like what you’re doing?
I think my case is a little bit special because it came organically and I’m branching out on my own at 40. That’s not for everybody. But if you want to be a footwear designer, I think there’s plenty of options and you don’t even have to start out as a footwear designer.
You do have to become a good designer in the sense that you can find inspiration that is surprising and you are able to communicate your ideas; that’s just the requirement for any designer. You need to be good at sketching, and it doesn’t matter if you do that with a pencil and paper or in 3D or whatever, but you’ve got to be able to wow with your ideas globally.
If you look at the market, a lot of current footwear designers want to be sneaker designers, which is totally okay. But maybe you shouldn’t be looking too much at a Nike and adidas and instead look at smaller brands that’ll give you way more potential early in your career to do fun stuff. You might look at a Decathlon, for example, or at the Chinese brands now that are doing great.
There might be a little bit of a gap in communication at the moment, but give it another five years, and those Chinese brands will be wanting an international team too, so I think that’s another great option that’s ideally suited for those wanting to get into design for mass production.
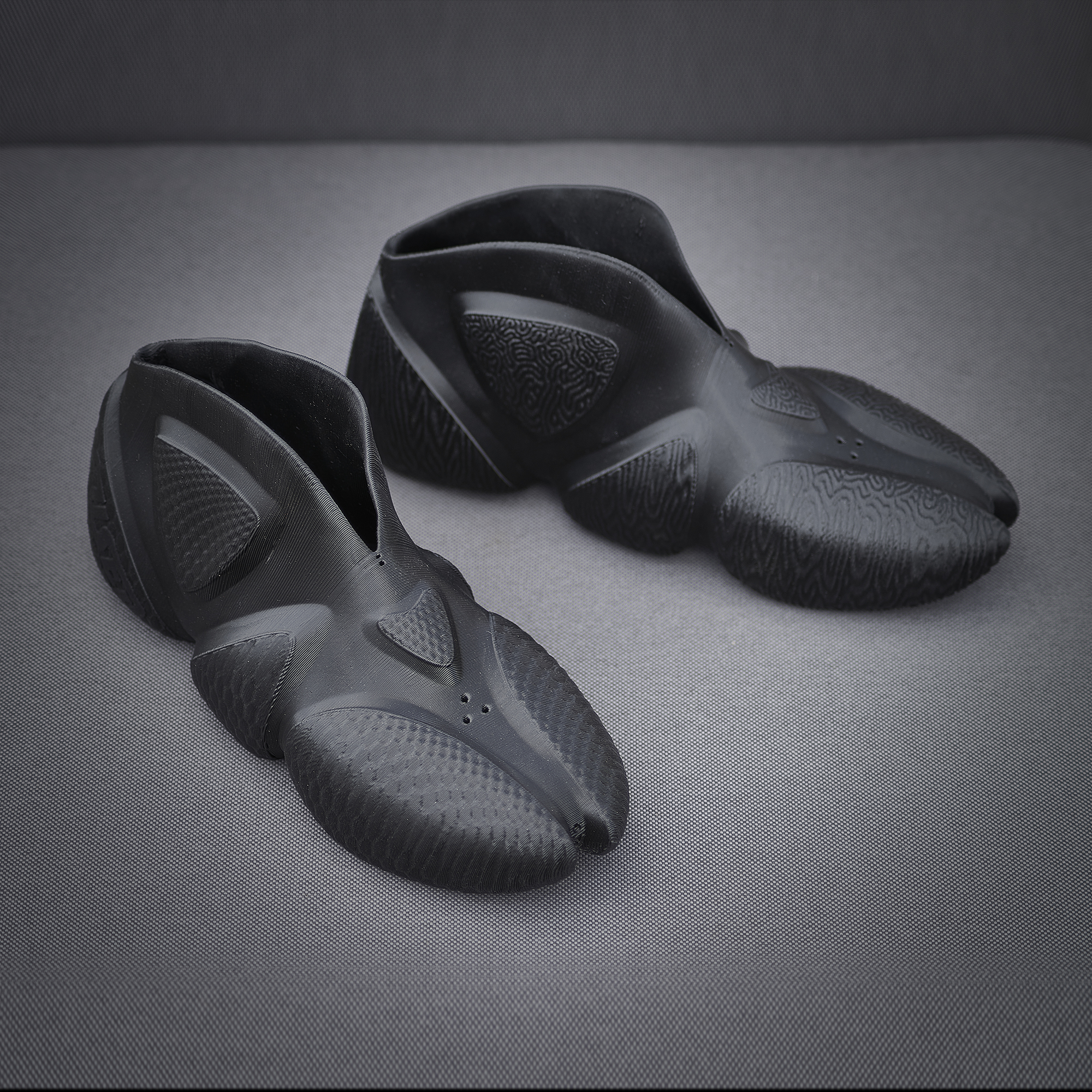
Sustainability
Given your goal of being able to recycle old pairs of FUSED footwear, what are your thoughts on sustainability, especially for the footwear realm?
I think if you’re thinking of developing a product and you can make a mono material product, you are doing something good for the world.
For one, it makes it easier to recycle, but second of all, with it being a mono material, you’re not using a lot of extra resources that you would use such as for transport or attaching several different materials together.
But as a consumer, nobody’s expecting you to start wearing only sustainable shoes all of a sudden. You can do that if that’s what you want to do, but I’d also ask you to be relatively broad minded about it.
If you buy a good pair of leather shoes, they can last you a lot longer than most sneakers. Although sneakers can be awesome and are awesome, if you buy a pair of Zara sneakers, you’re making it worse in some way because this is a consumer product that was made at a very low price and in very large quantities.
Ideally, you want to go for sneakers that are a little bit more special. It doesn’t have to be the most expensive ones, but if something is made in lower volumes, that would maybe get the suppliers to think “what are we really doing? Do we want to make mass-market shoes or do we want to make small volume shoes?” If you do small volume, you have to think a little bit further. There are so many options to consider how a shoe is being made.
Of course, a lot of brands are also using this purely as a greenwashing marketing trick and that is something you always need to be aware of as well. For instance, the Adidas 4D mid-sole is super cool, but it really doesn’t use any of the great benefits that 3D printing offers. It’s just something that looks cool, but it’s not better than their Boost midsoles. It’s heavier, and potentially more polluting because the 3D printing process that they use is not recyclable, which is another thing to keep in mind. So especially if you’re an aspiring designer, my advice is to feel free to push back a little bit on the higher-ups.
On the other hand, I saw that another brand just came out with a fully natural shoe, which is also very interesting. It had a hemp upper and natural dyes and natural latex. They were a little bit too eco for me, so although they don’t look super cool yet, we’re getting there and I think there’s plenty of good intention in the industry.
As someone who makes technical footwear, Philippe shares his views on techwear and his own style.
How would you personally assess purchasing more eco-friendly shoes?
Ideally, you want to go for sneakers that are a little bit more special. It doesn’t have to be the most expensive ones, but if something is made in lower volumes, that would maybe get the suppliers to think “what are we really doing? Do we want to make mass-market shoes or do we want to make small volume shoes?” If you do small volume, you have to think a little bit further. There are so many options to consider how a shoe is being made.
Of course, a lot of brands are also using this purely as a greenwashing marketing trick and that is something you always need to be aware of as well. For instance, the Adidas 4D mid-sole is super cool, but it really doesn’t use any of the great benefits that 3D printing offers. It’s just something that looks cool, but it’s not better than their Boost midsoles. It’s heavier, and potentially more polluting because the 3D printing process that they use is not recyclable, which is another thing to keep in mind. So especially if you’re an aspiring designer, my advice is to feel free to push back a little bit on the higher-ups.
On the other hand, I saw that another brand just came out with a fully natural shoe, which is also very interesting. It had a hemp upper and natural dyes and natural latex. They were a little bit too eco for me, so although they don’t look super cool yet, we’re getting there and I think there’s plenty of good intention in the industry.
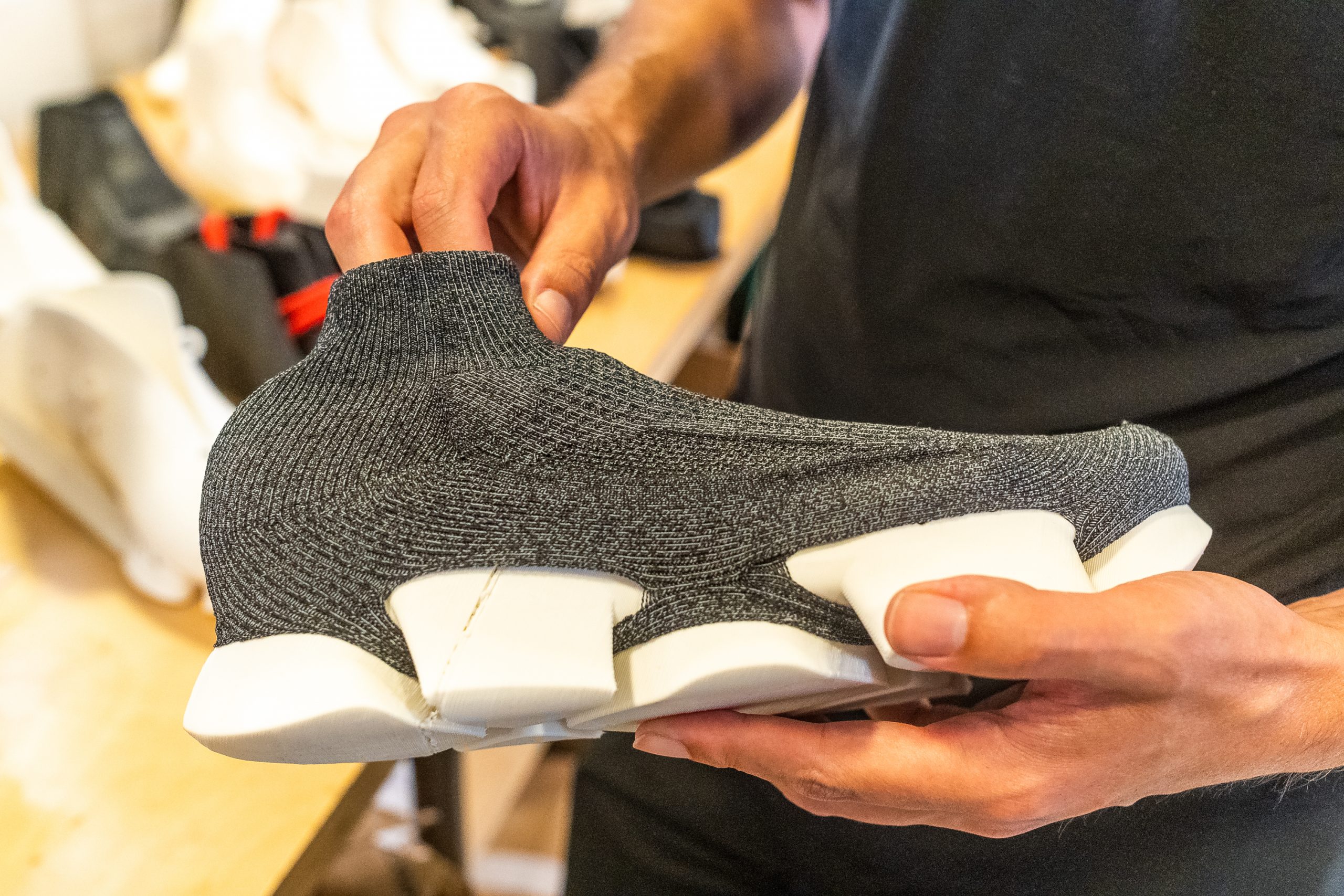
Philippe’s experiment with adding a knitted cover over a 3D-printed shoe.
What Comes Next
Are there any new silhouettes on the horizon?
What other projects are you working on that you’d like to shout out?
There are few brands that I really really hope to collaborate with at some point. Talks are already happening, but these folks are all in a similar position, running passionate but small brands:
PetersonStoop, we are planning to put a FUSED 3D printed cupsole on their restored sneakers, attaching them by stitching only, so they can be easily replaced in the future.
ShoeArtistry, they do made-to-measure leather dress shoes, and we are working on a brand that will combine their beautiful leather uppers with a 3D printed galosh type outsole.
Zellerfeld, these guys are in Germany and have built a footwear-specific 3D printer. They are on another level of refinement, and are my go-to once I need to scale up production.
And I’ve been chatting with a young local fashion designer, Tomy Ng, who would like some shoes to go with his new collection. That should be a fun project too!
“The products that I make in the end, I want people to do double takes. You see somebody wearing FUSED Footwear, and you go ‘what is he — what does he have on his feet? Where did that come from? Where can I get that potentially?’
But I also want it to be strange enough that the majority of people will go, ‘I can’t wear it. It’s too weird.’”
— Philippe Holthuizen